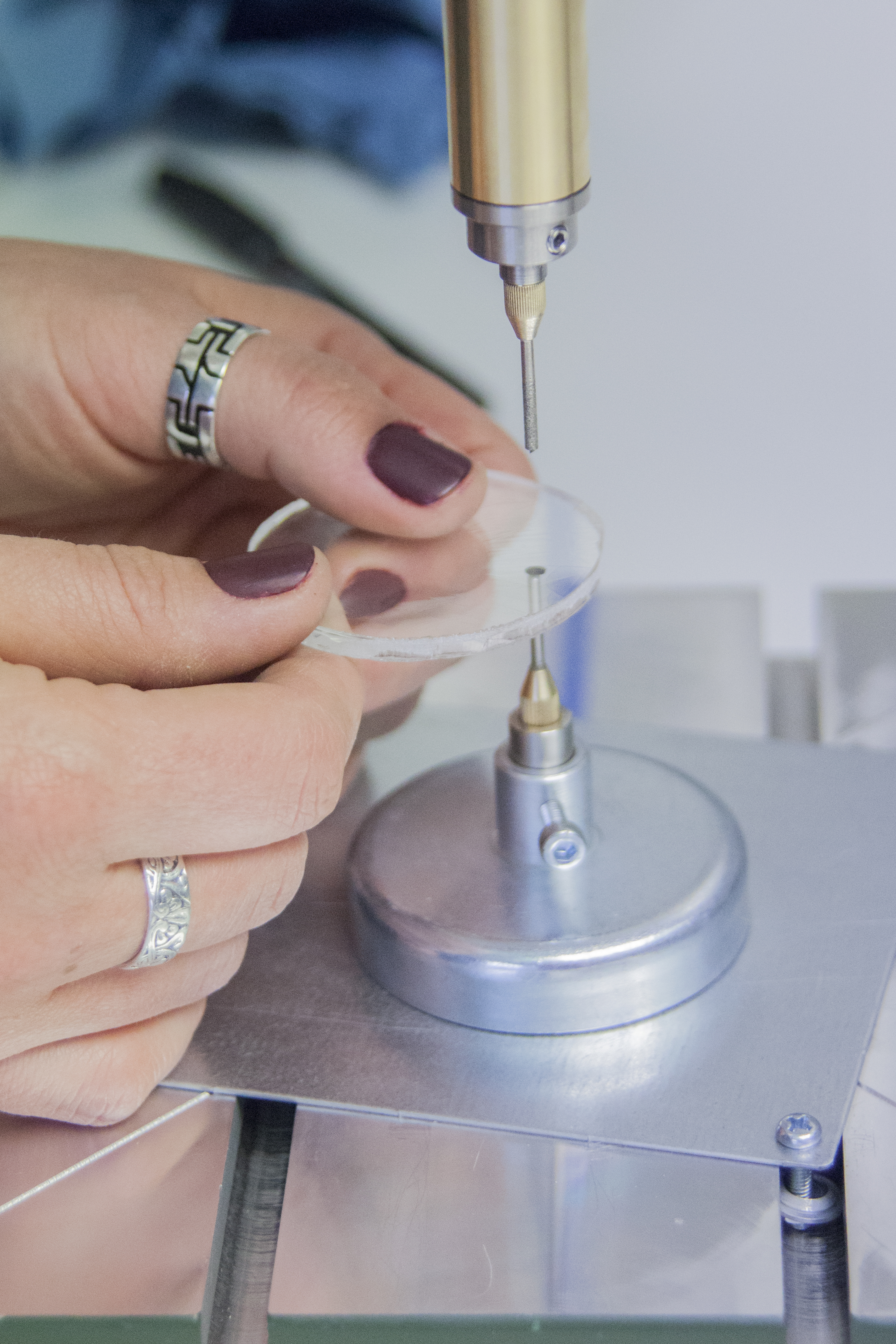
Diamond hollow drilling spindle with automtaic core ejector Item No. 3027000-3027381
The handling of the diamond hollow spindle is very easy, because every conventional drilling machine is suitable as a working device. The prerequisite is, however, that the spindle runs smoothly after insertion in the machine and that it does not wobble. If the spindle in the sprocket lining does not run smoothly, switch to a quick-action chuck.
Step 1
On the spindle there is a water connection with a union nut on the side. This please turn down, pass the existing blue water hose through the union nut and plug it into the side water connection. Then screw on the union nut again. The same thing is done at the existing water connection, which is turned on the faucet.
If you use the pressure pump: At this the blue hose is already mounted. You only need to connect it to the spindle.Insert the diamond hollow spindle into the existing drill chuck of the respective drill.
The water pressure should be min. 2 max. 6 bar. P.S .: A slight heating of the hose makes it easier to put it onto spindle & water connection !!!.
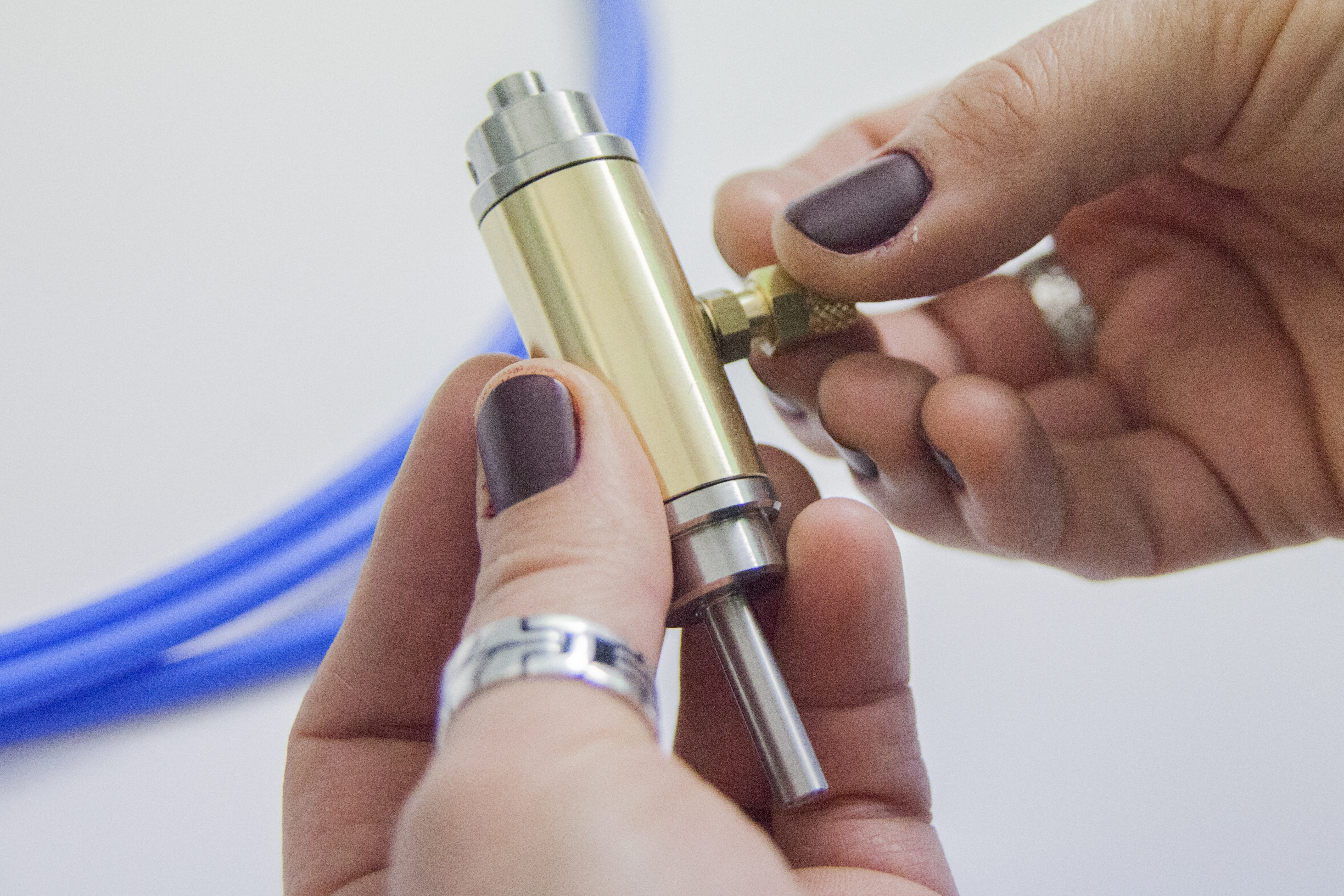
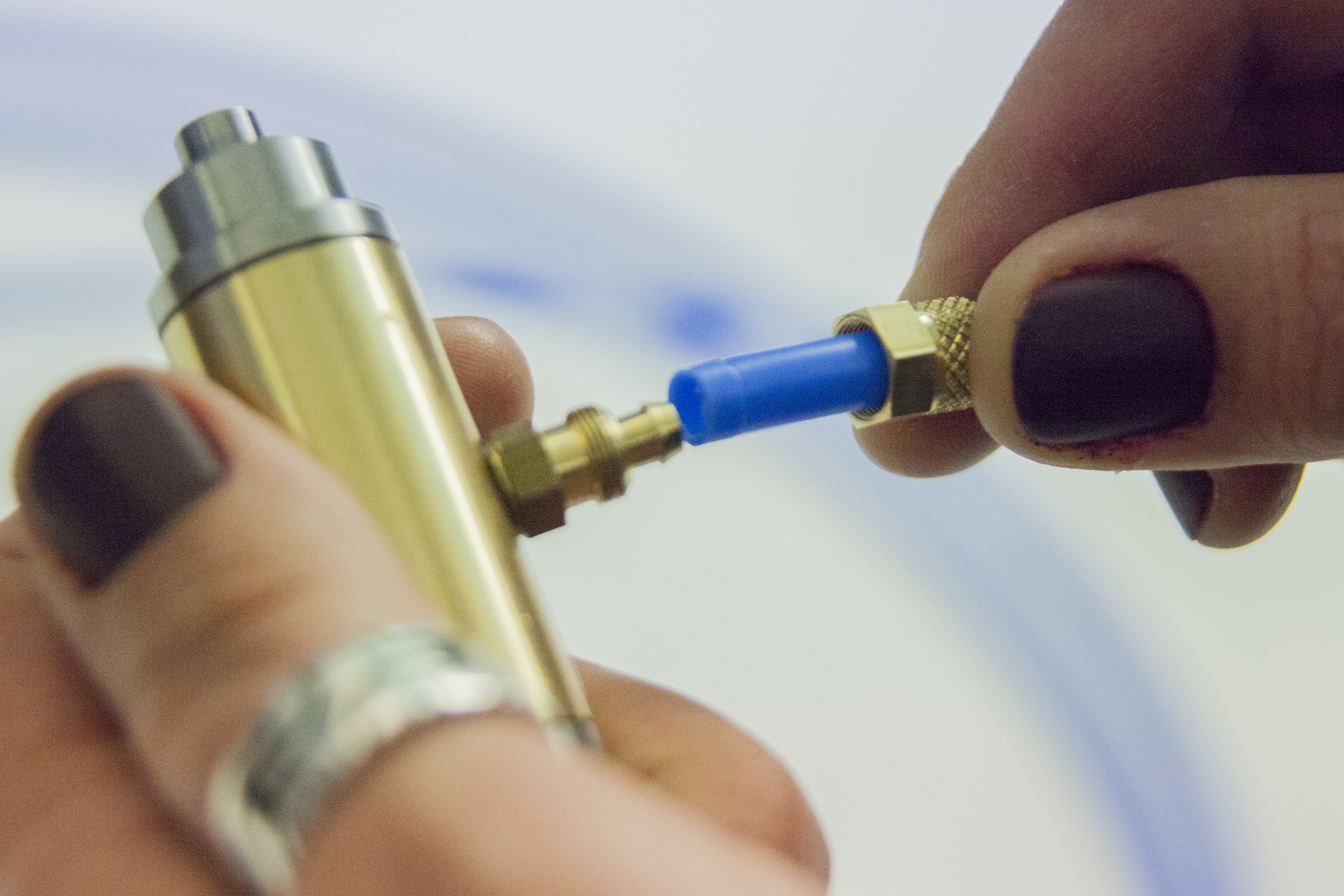
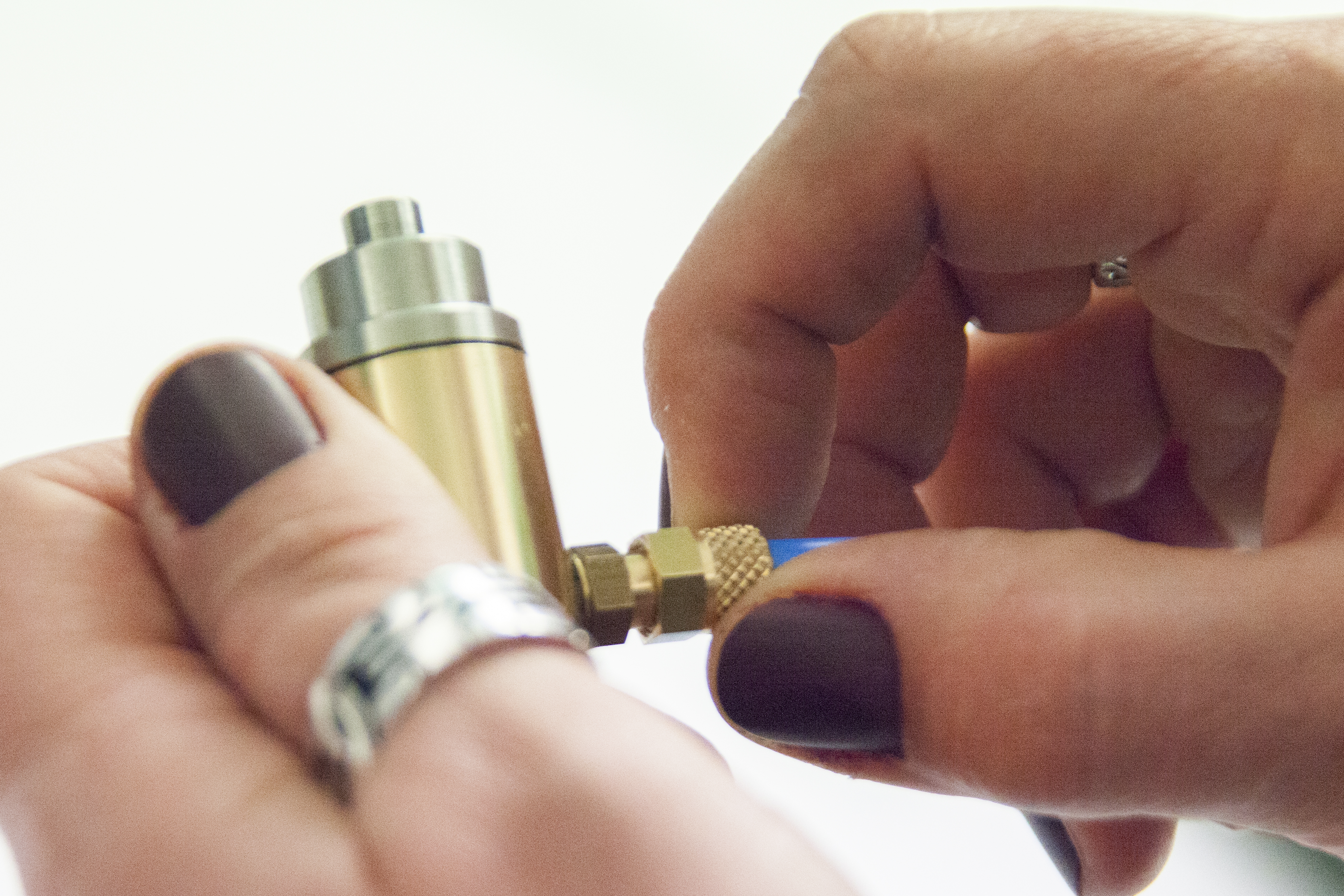
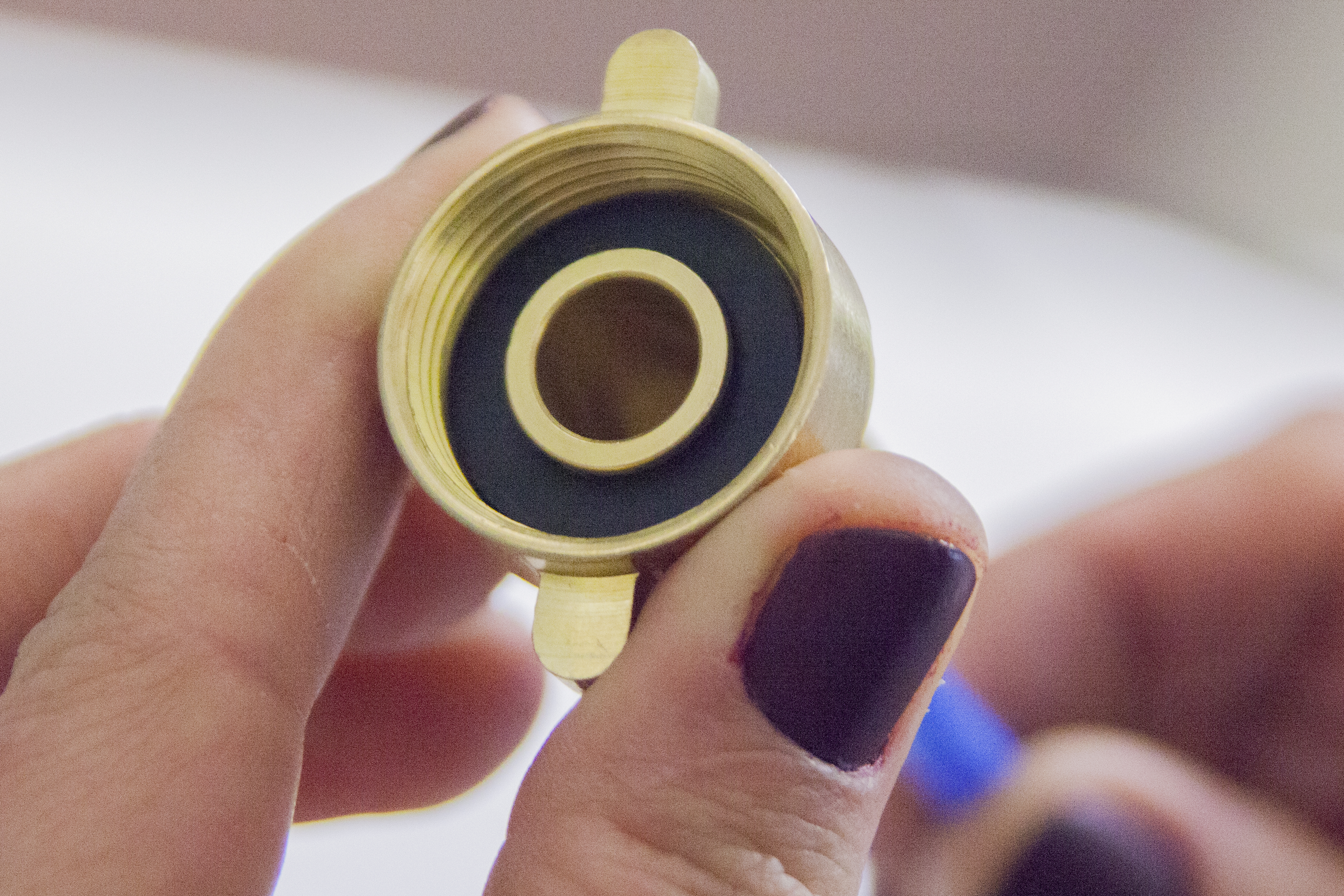
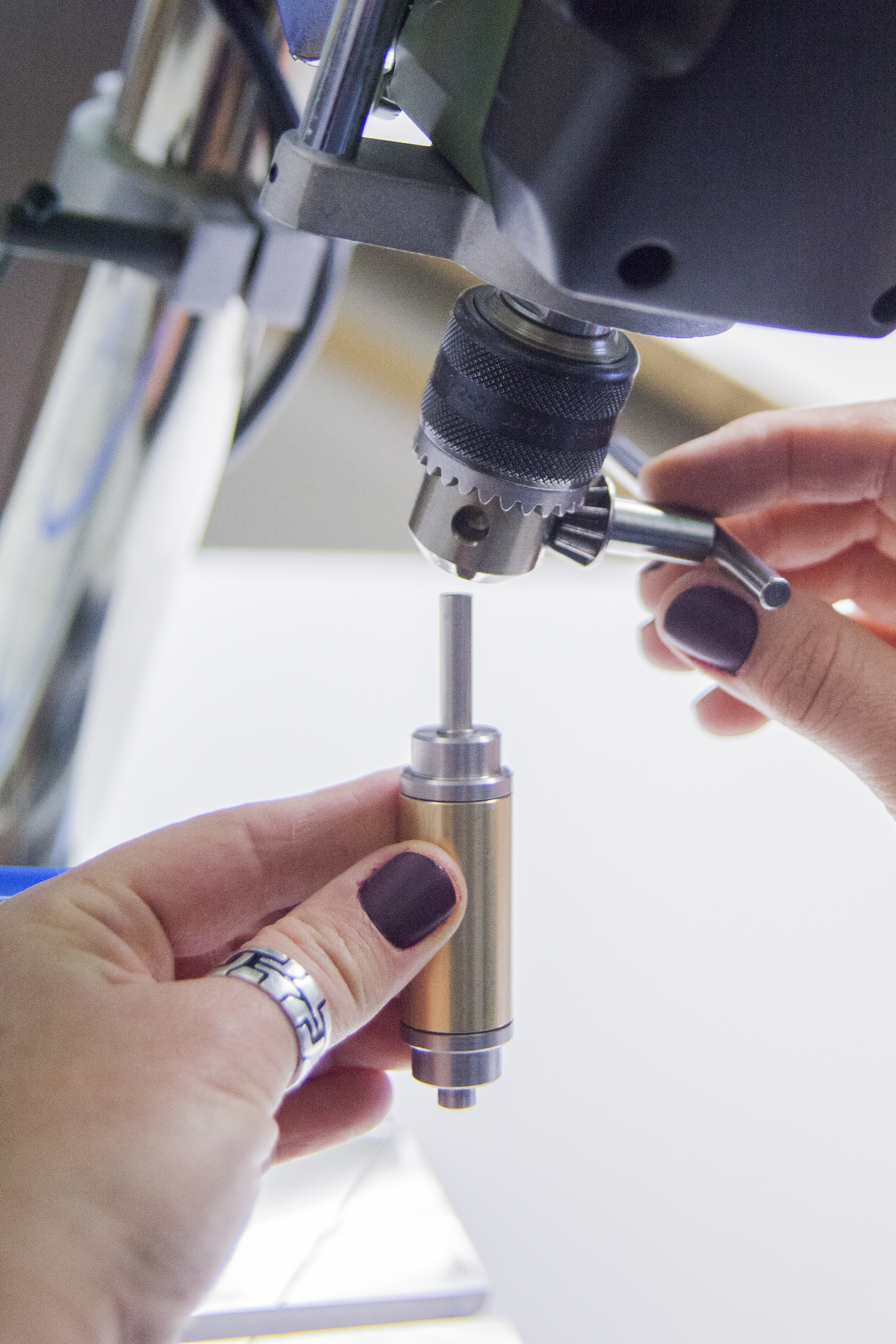
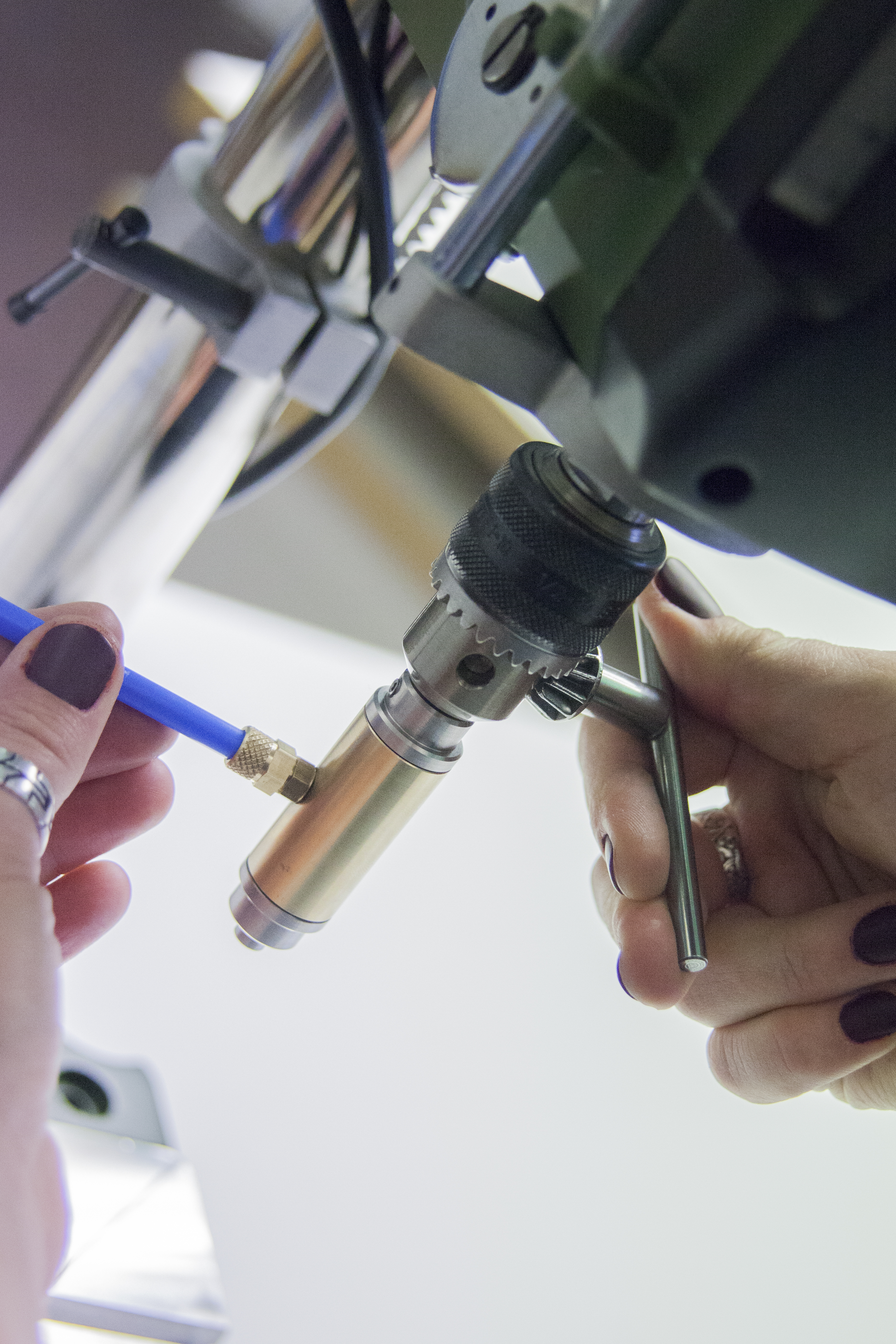
Step 2
Now you can take a desired diamond drill. In this there is an ejection needle. Insert the drill with this ejector needle into the spindle. Press lightly upwards and let the thread „bite“. Tighten the drill bit to the end and, if necessary, carefully tighten the drill bit with pliers to the spindle.
The ejector needle is usually supplied in the appropriate length in the drill. Nevertheless, drill and ejector are two different items. Slight differences in length with the same drill diameters are possible due to the production. It is possible that an ejector needle has not been „tuned“ to the drill bit. If so, please cut the needle so that it is about 1 to 2mm longer (when inserted) than the drill, and looks out.
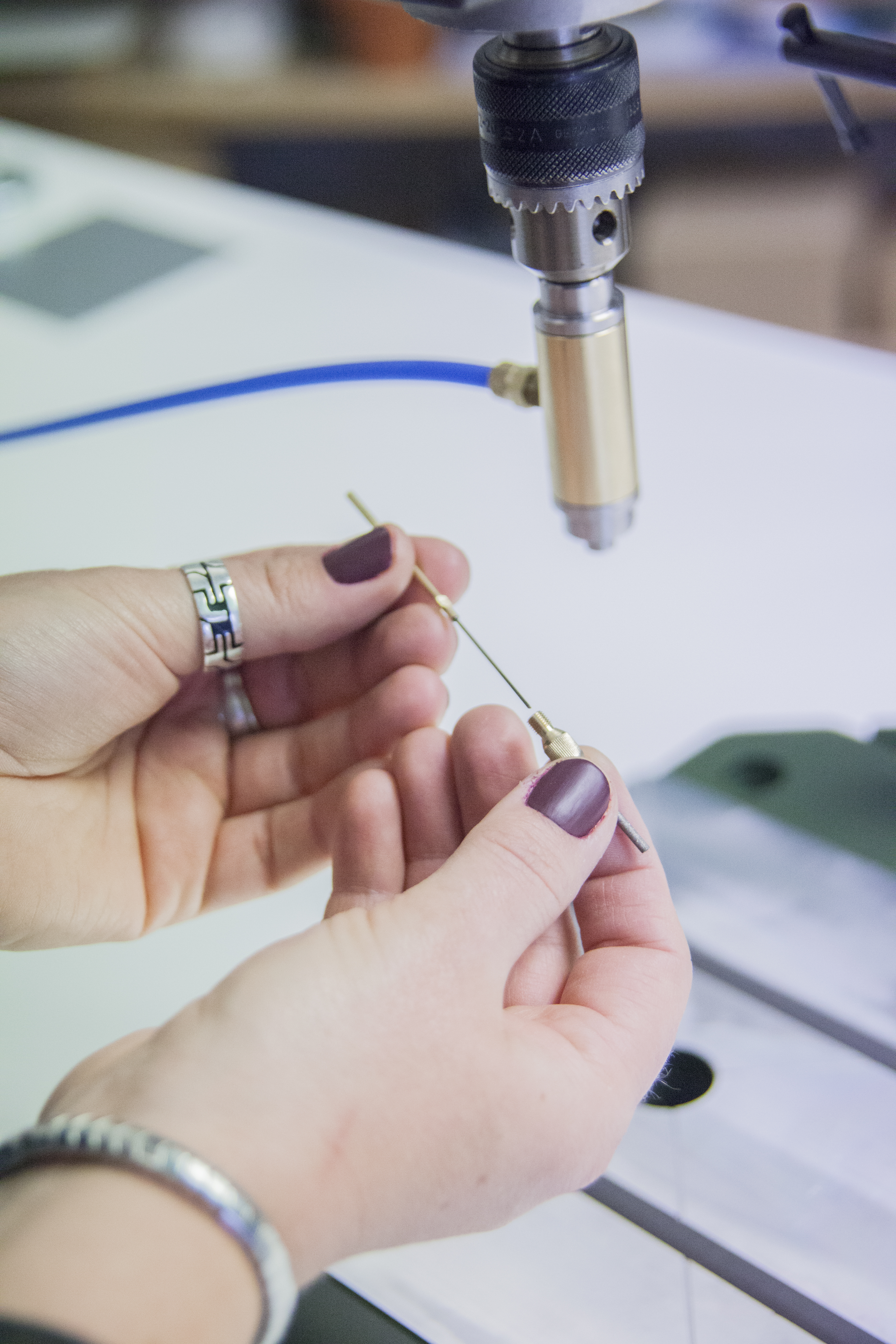
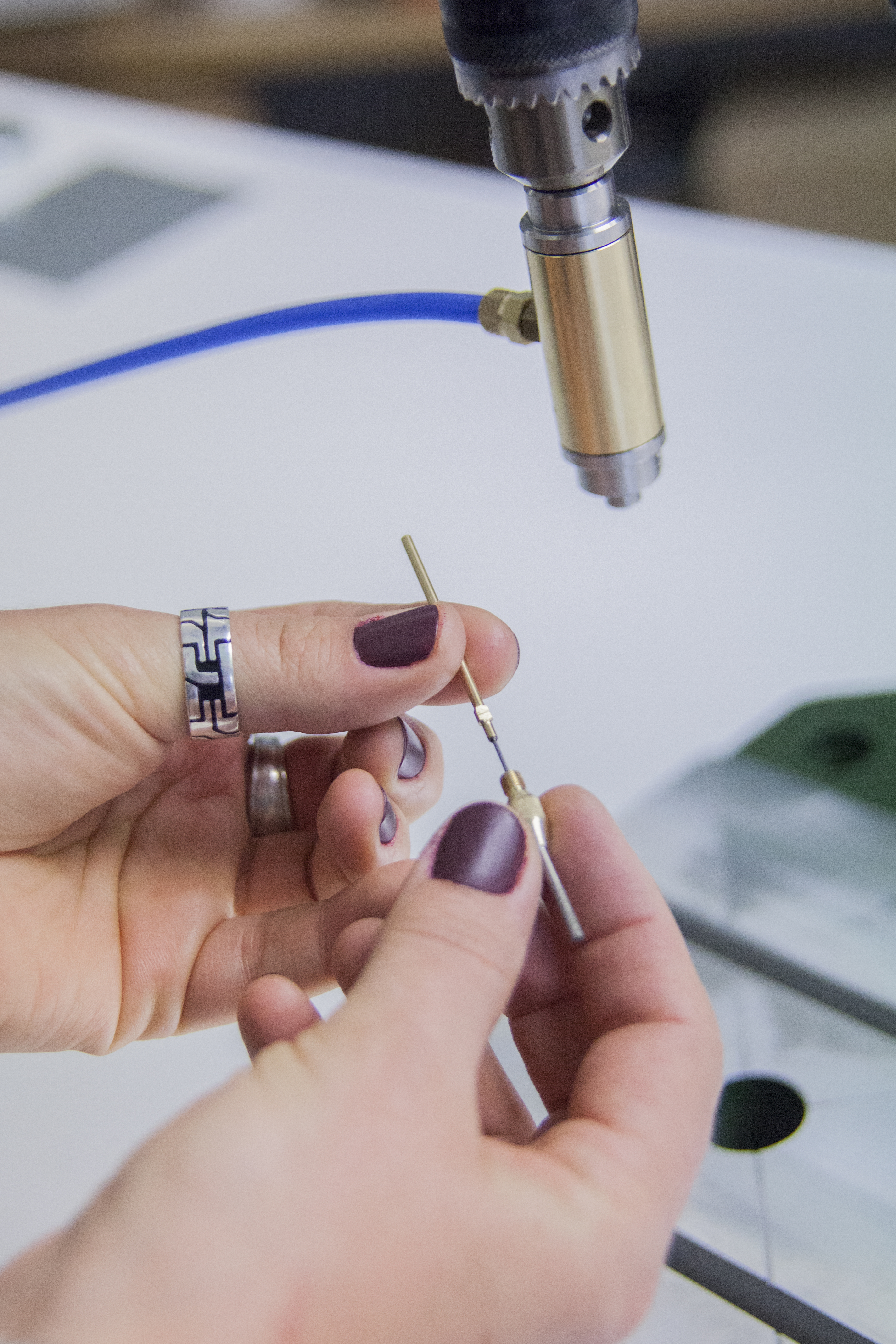
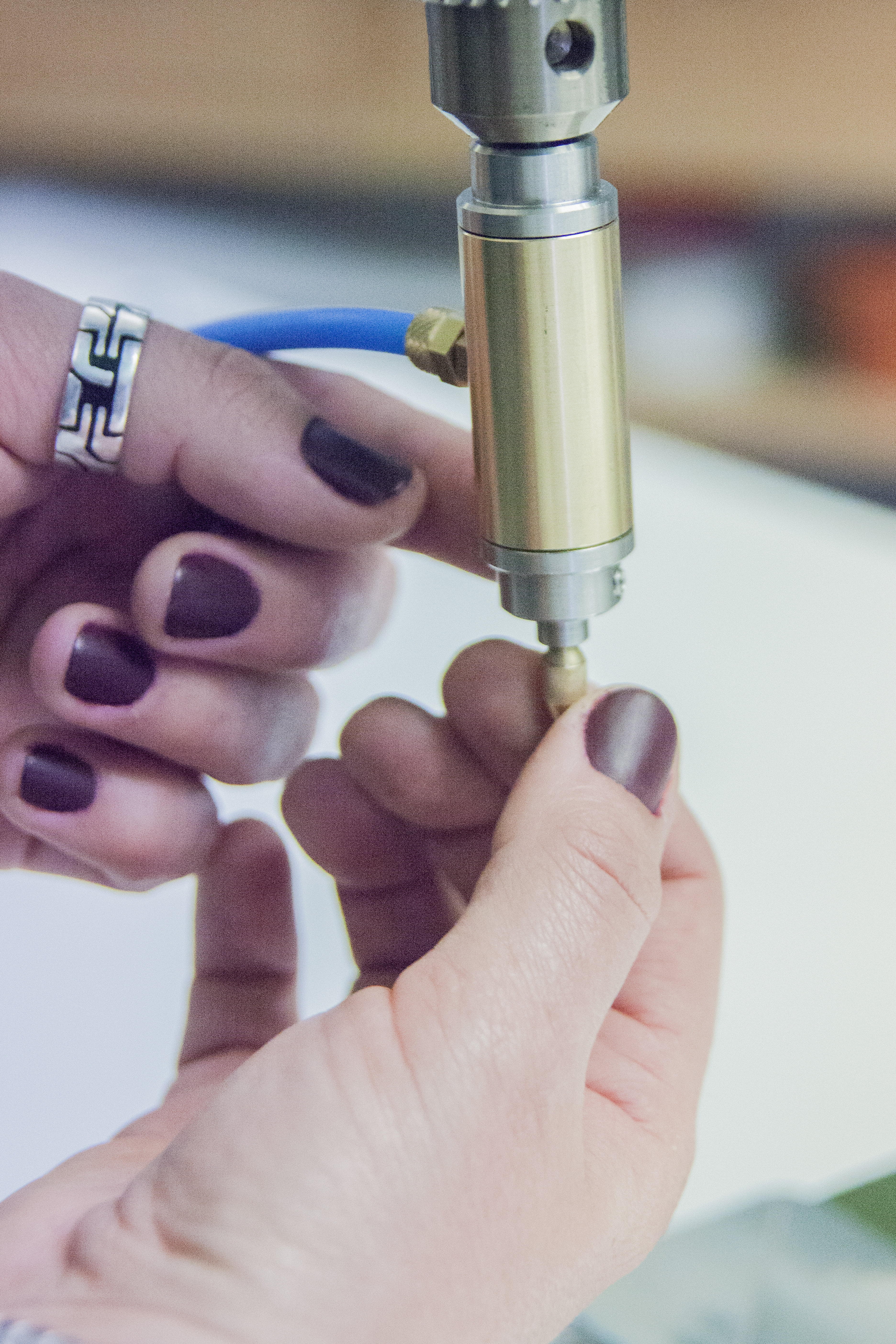
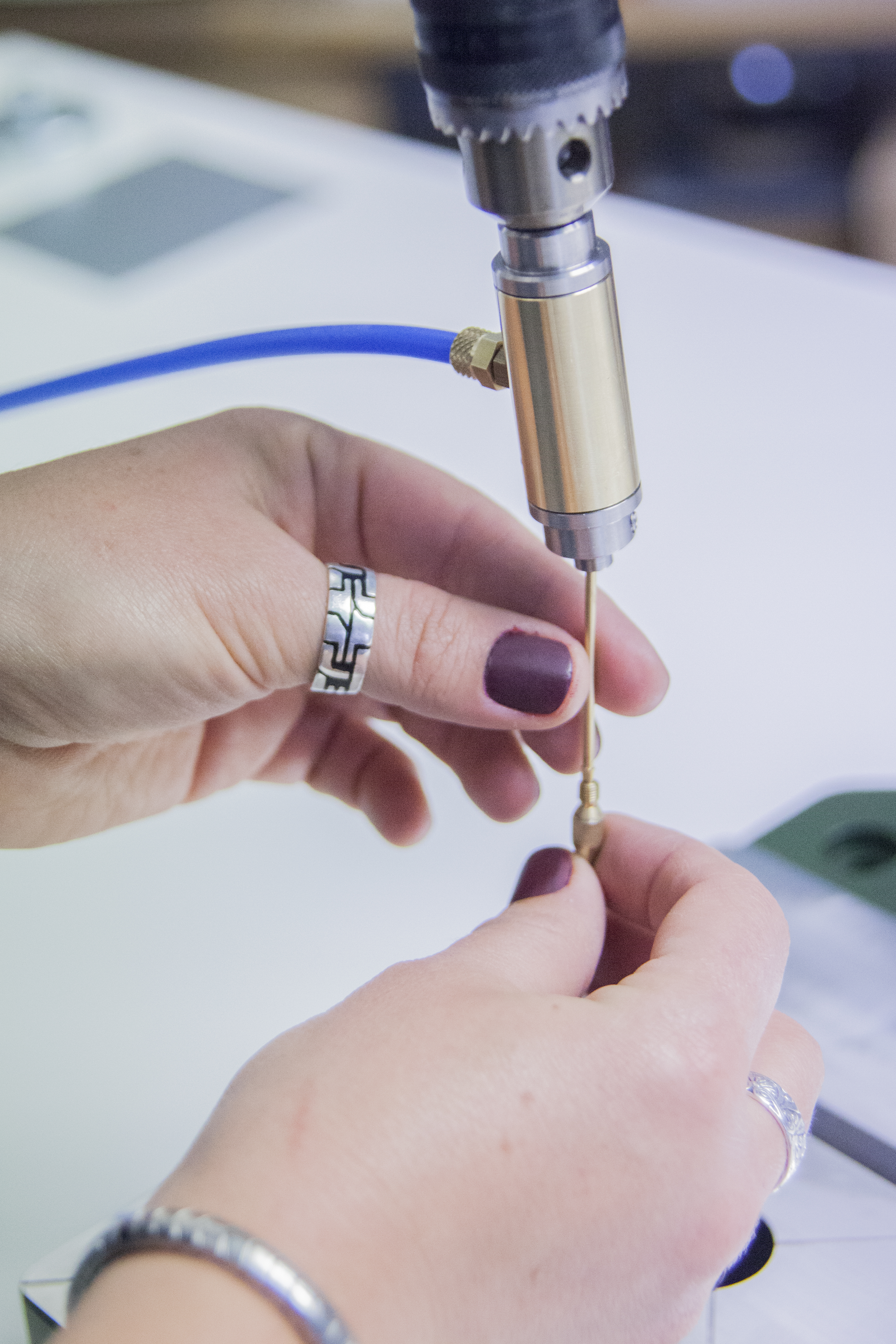
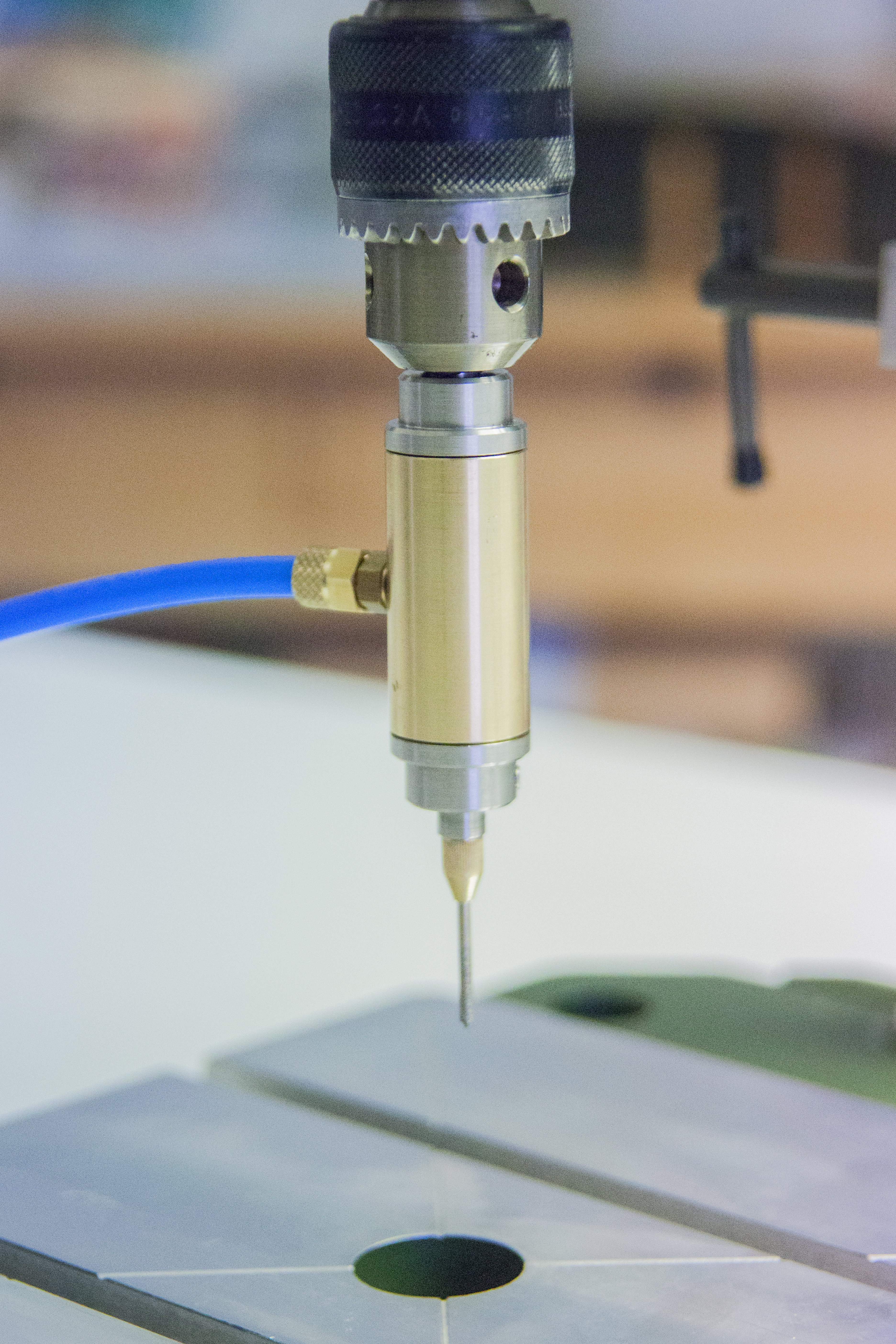
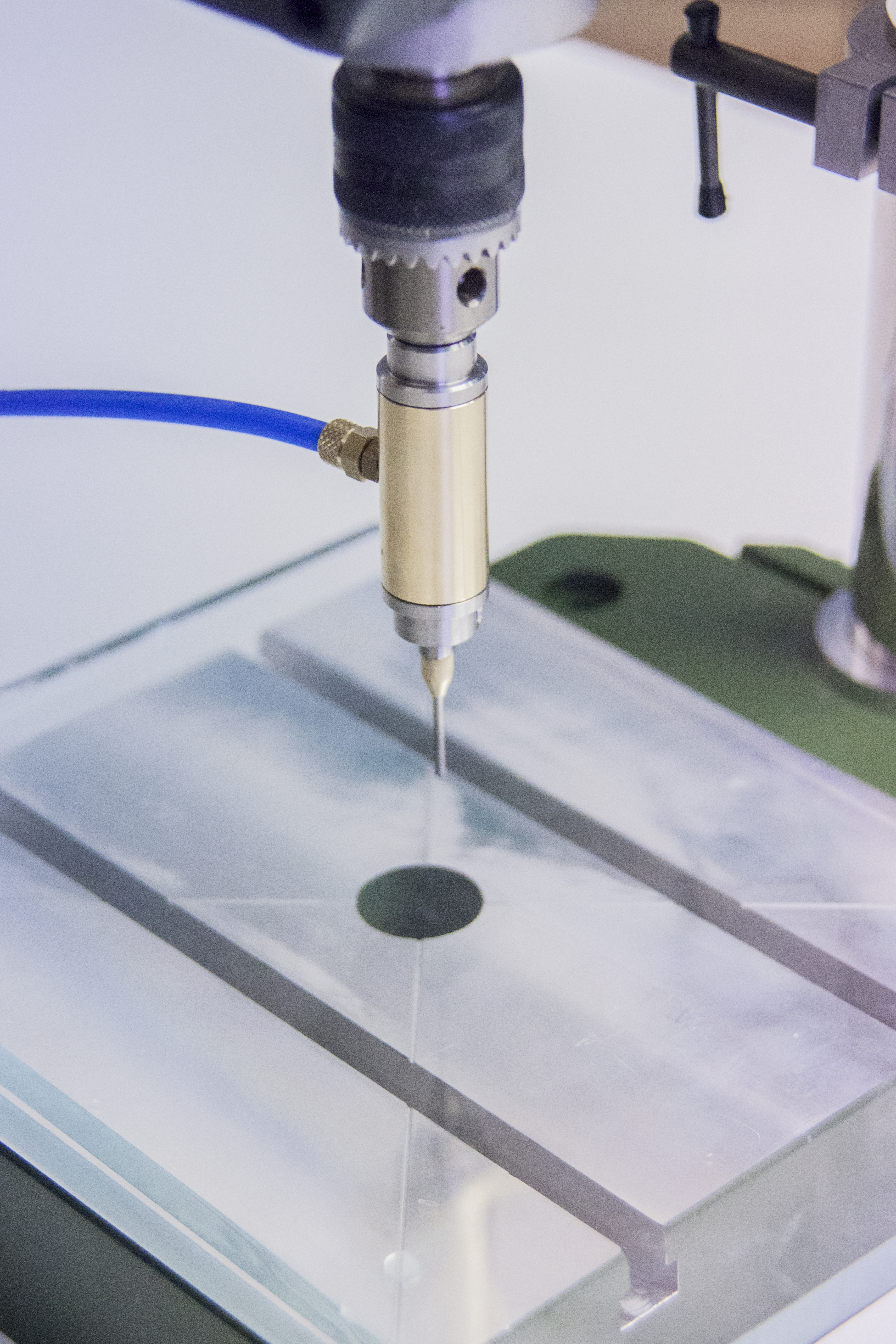
Step 3
Now you can mark the hole on your piece of glass and drill the hole. Important: Do not drill through completely. The advantage of this drilling system is the magnetic base with counterpart. This does not break the glass on either side. Adjust the depth stop of the drill appropriately.
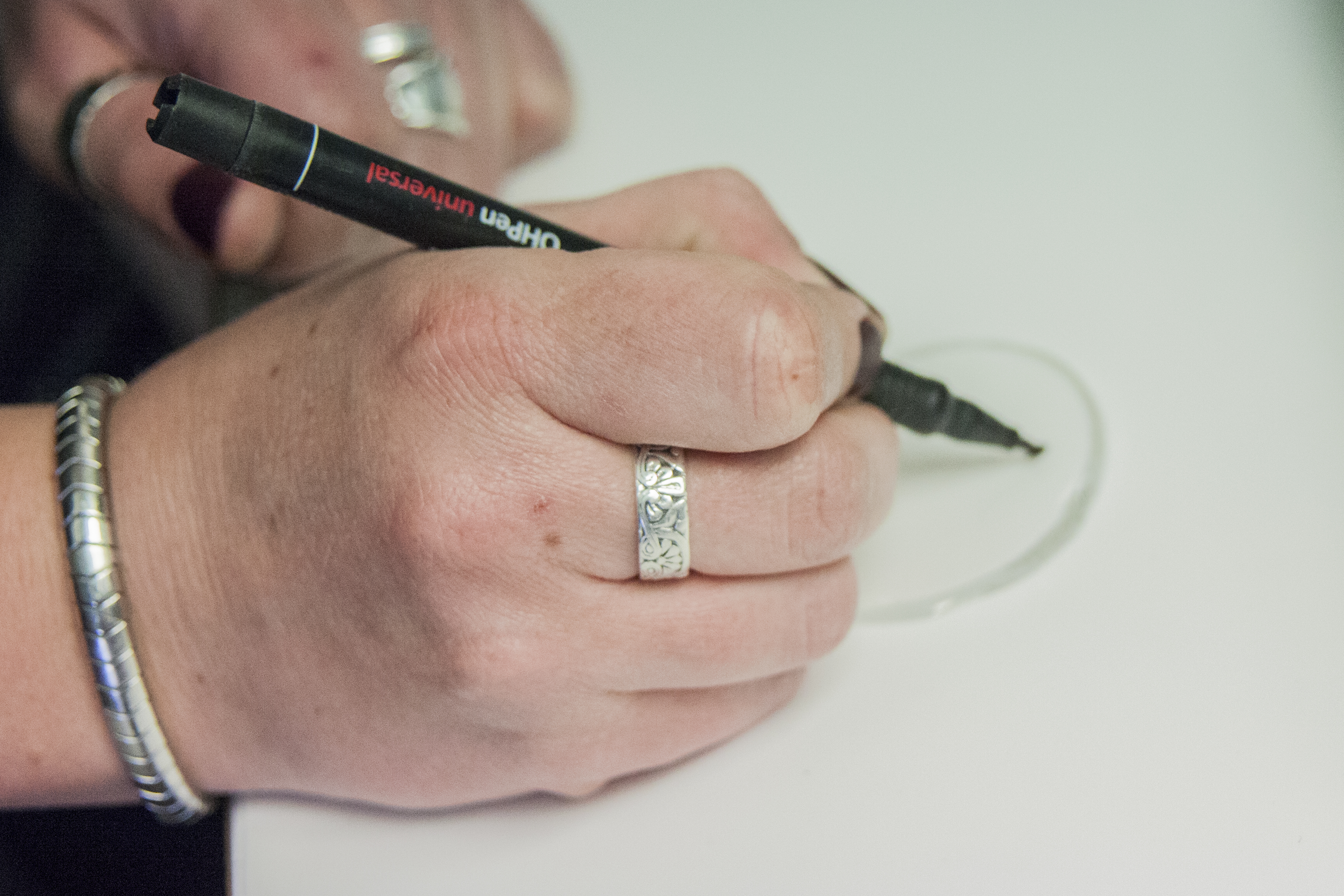
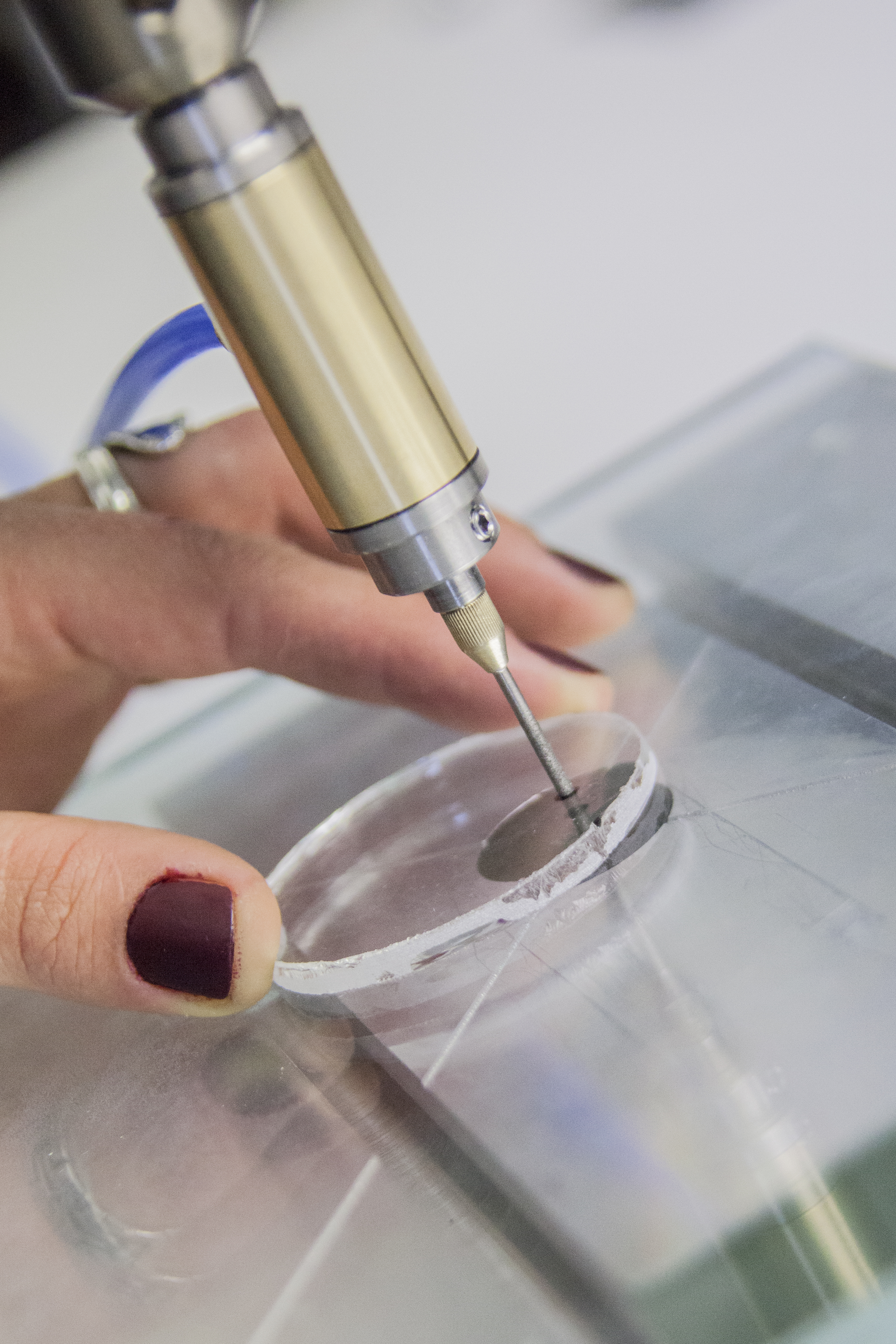
Step 4a
Magnetic base, metal plate, metal insert & counterpart: To prevent the drill core from breaking, the glass piece should always be drilled from 2 sides become. Place the magnetic base on the drill table. Then the metal insert is put into the magnetic base. If you want to drill a 2mm hole, take the matching counterpart, which is slightly thinner than the drill, about 2-3 tenths and turn this into the metal insert.
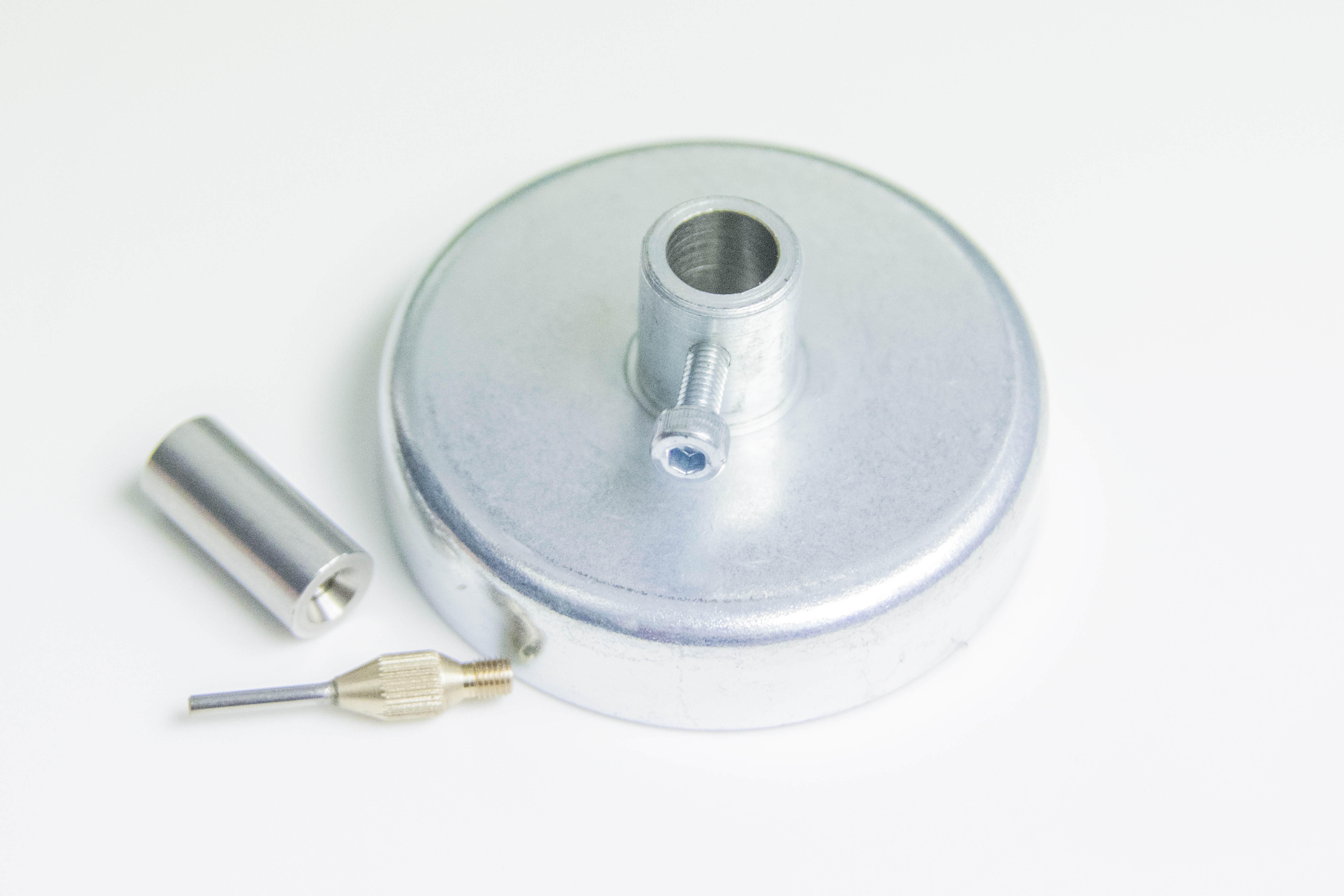
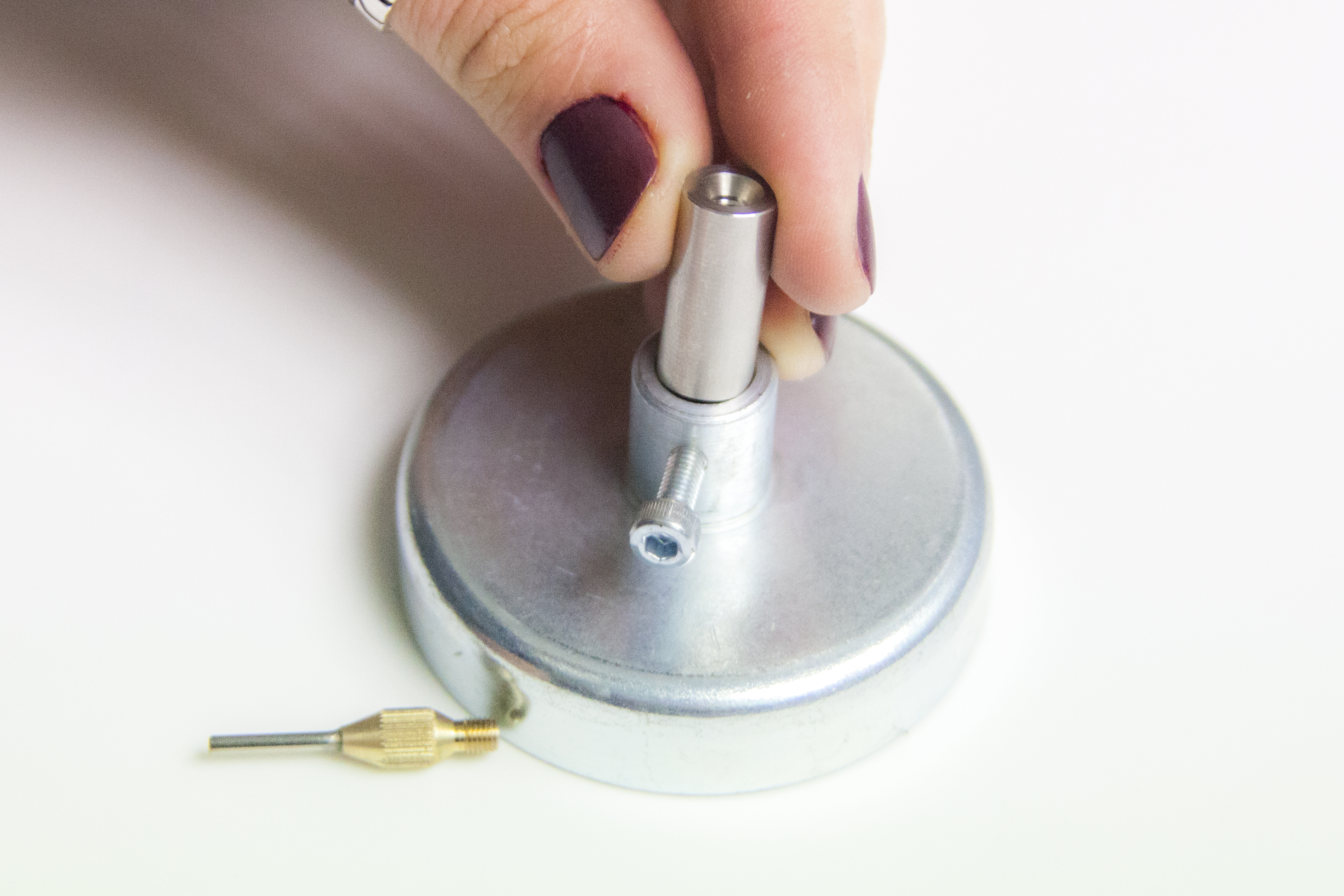
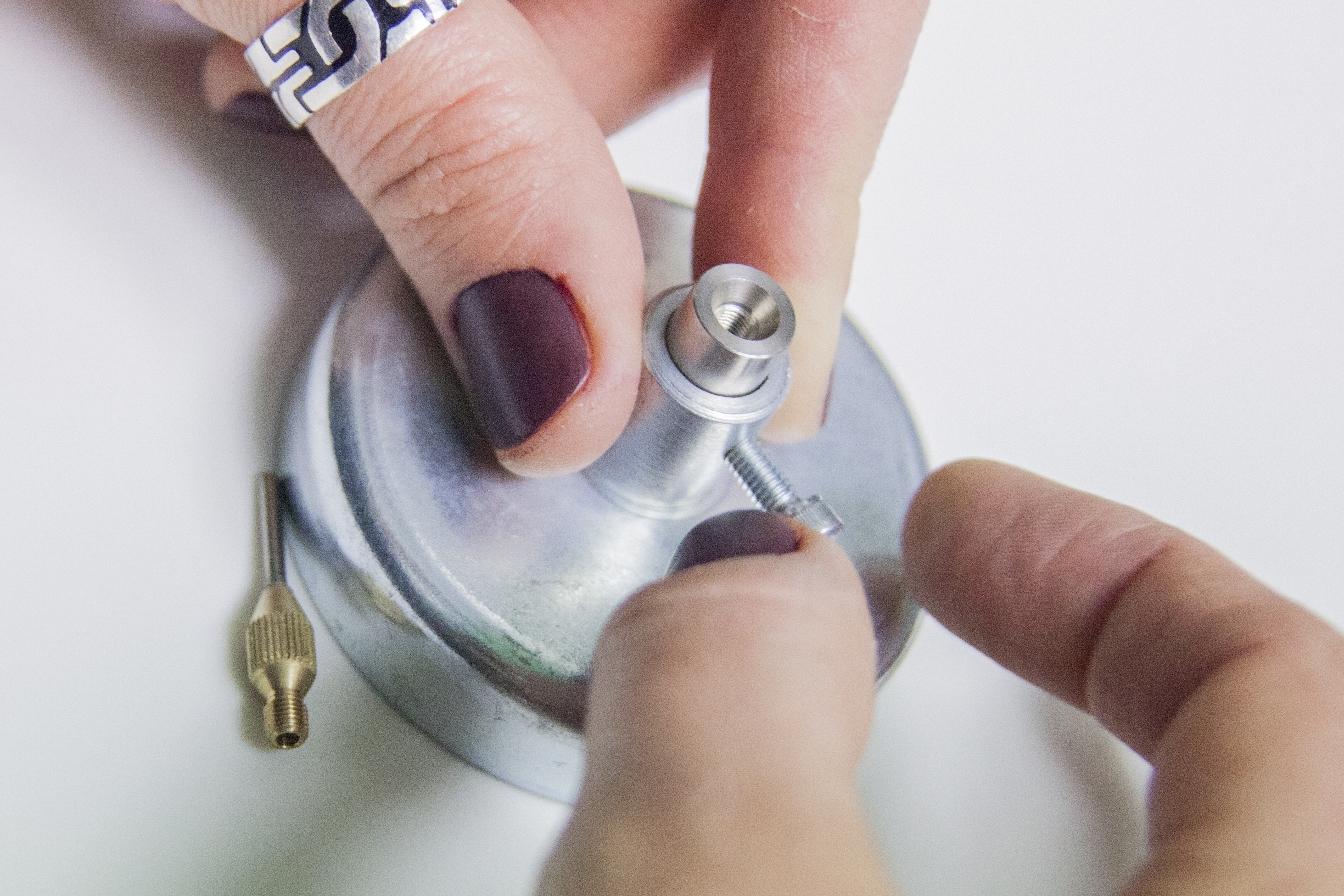
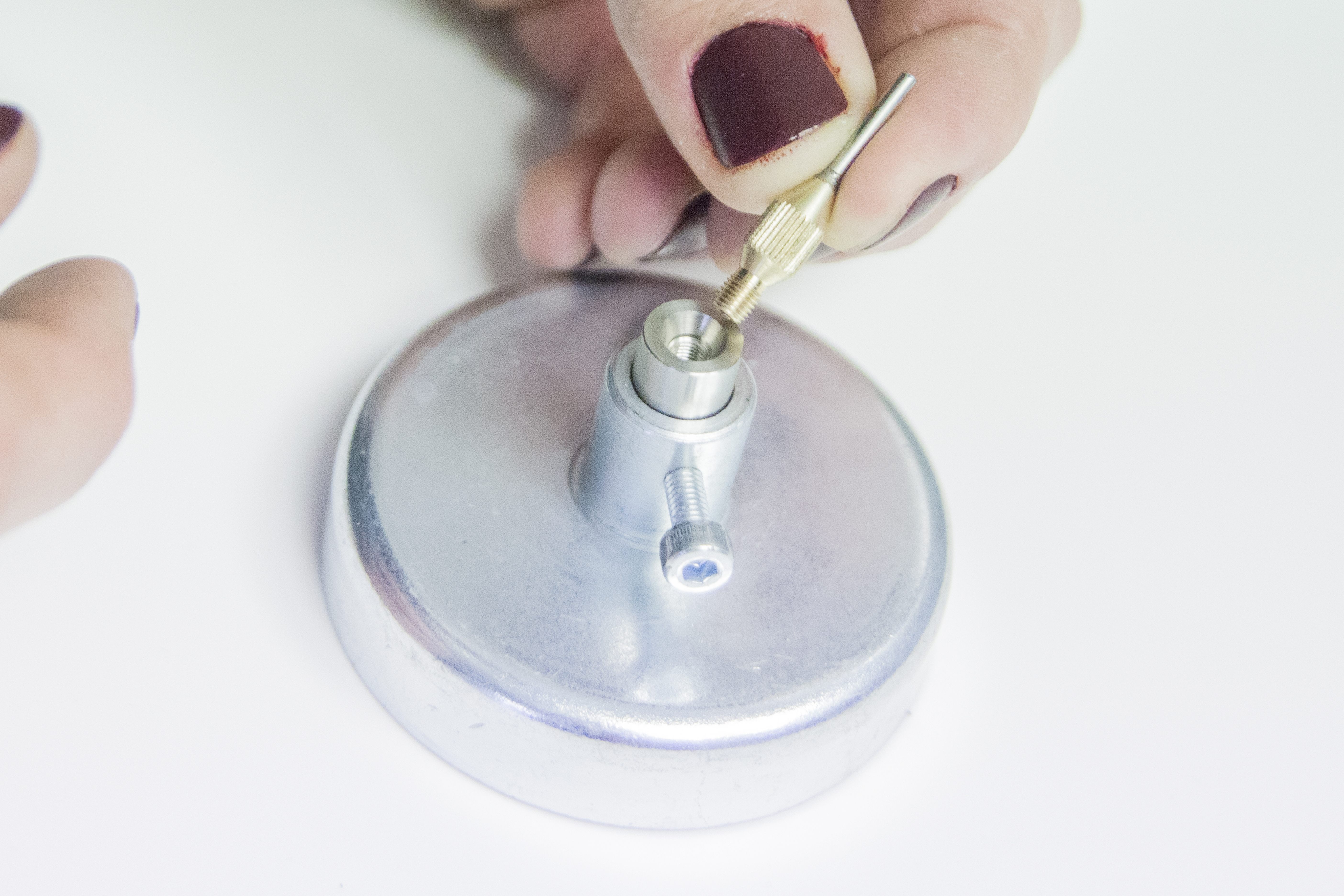
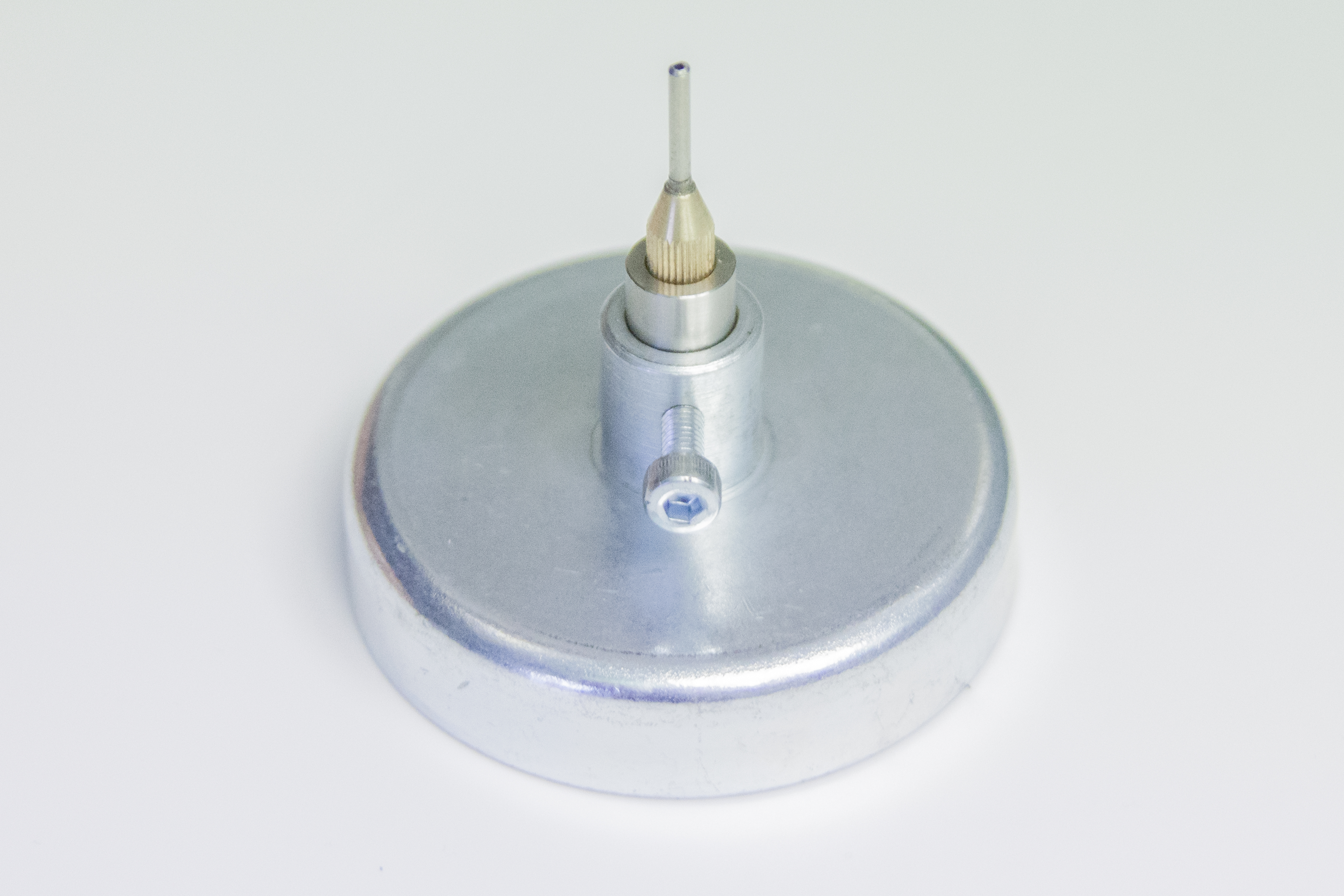
Step 4b
Then the magnetic base with the counterpart must be aligned exactly under the drill. For machines that have a metal base you can put the magnetic base directly under the drill.
For machines with an aluminum base (for example PROXXON machine) we offer a metal plate which can be screwed onto the drill foot.
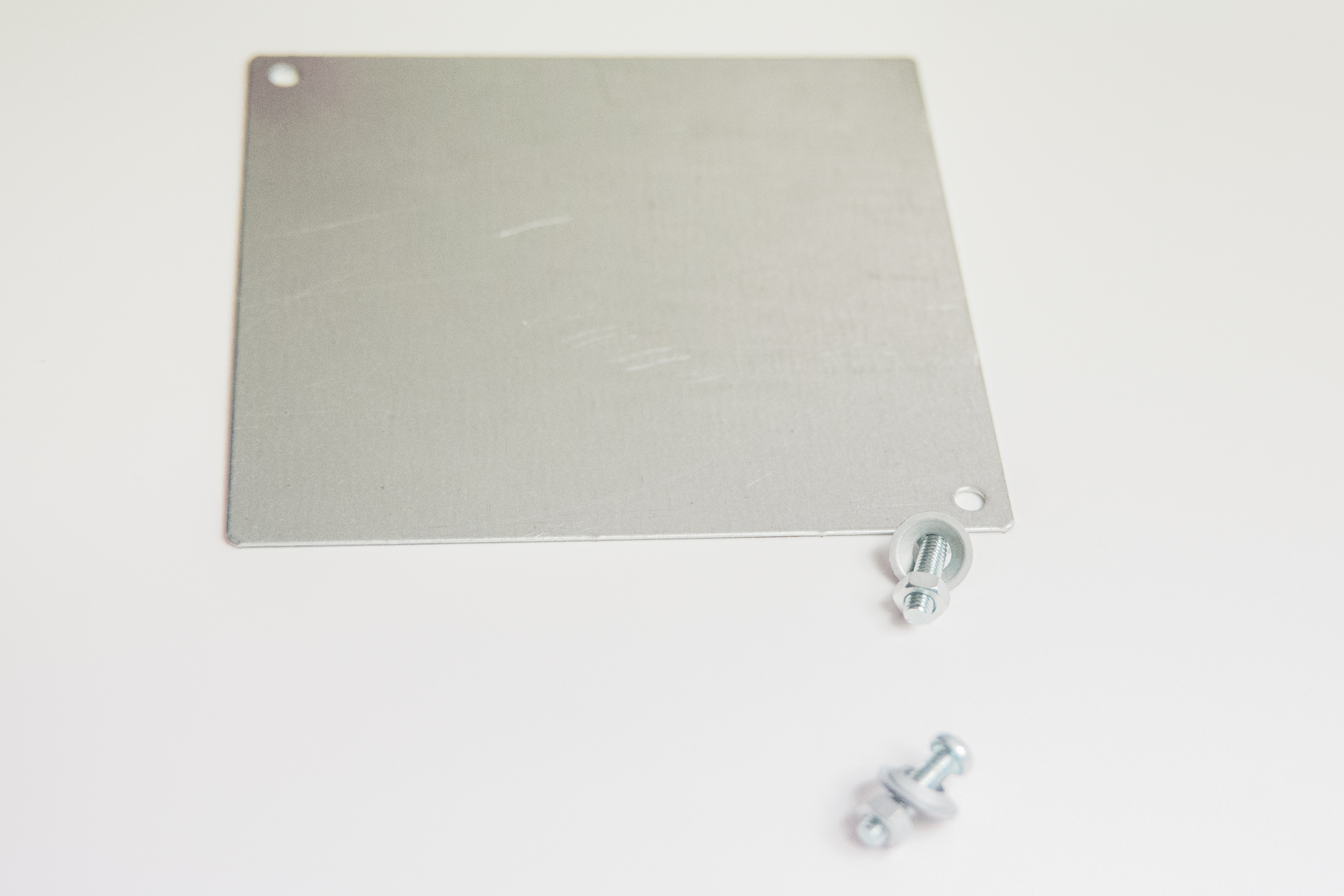

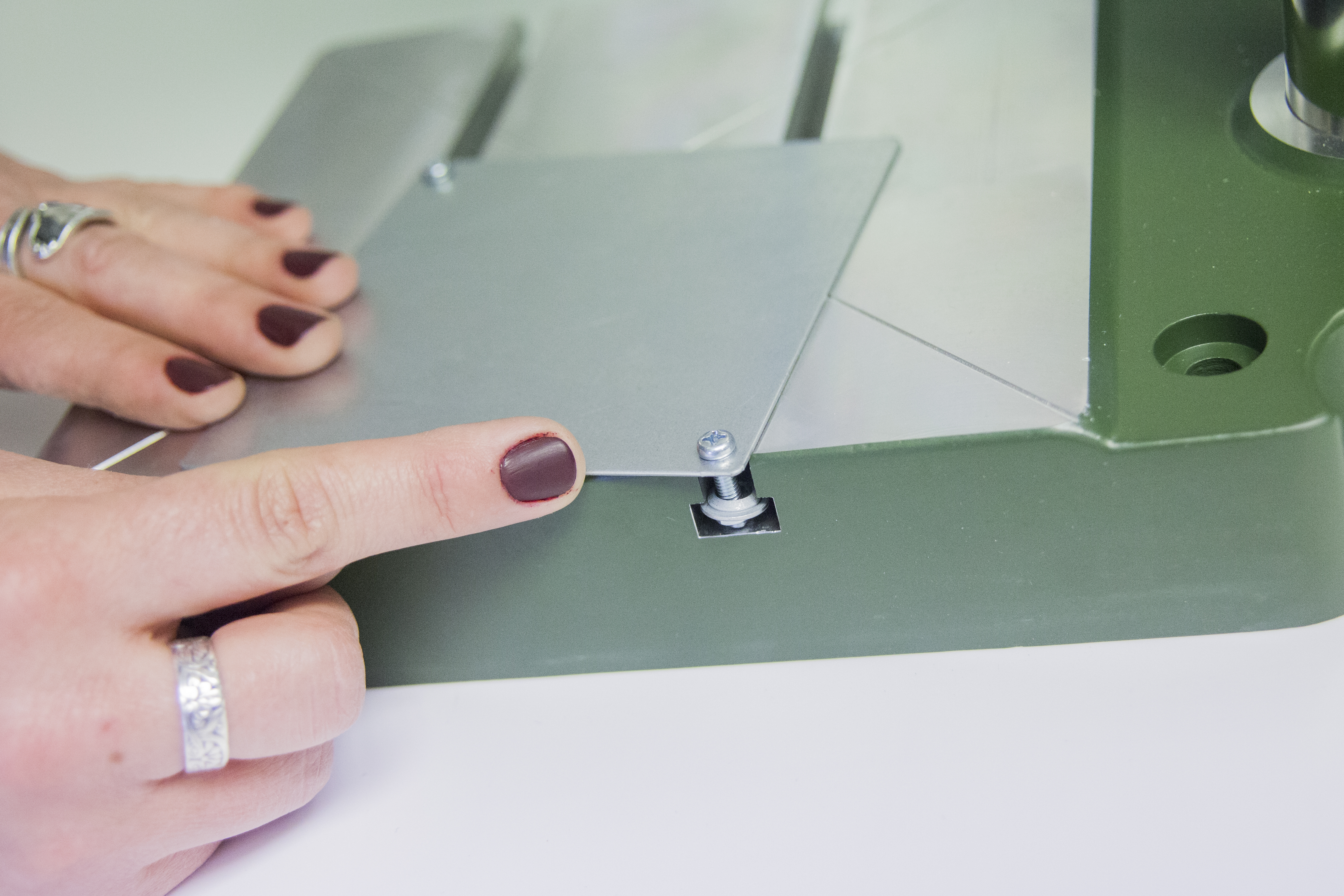
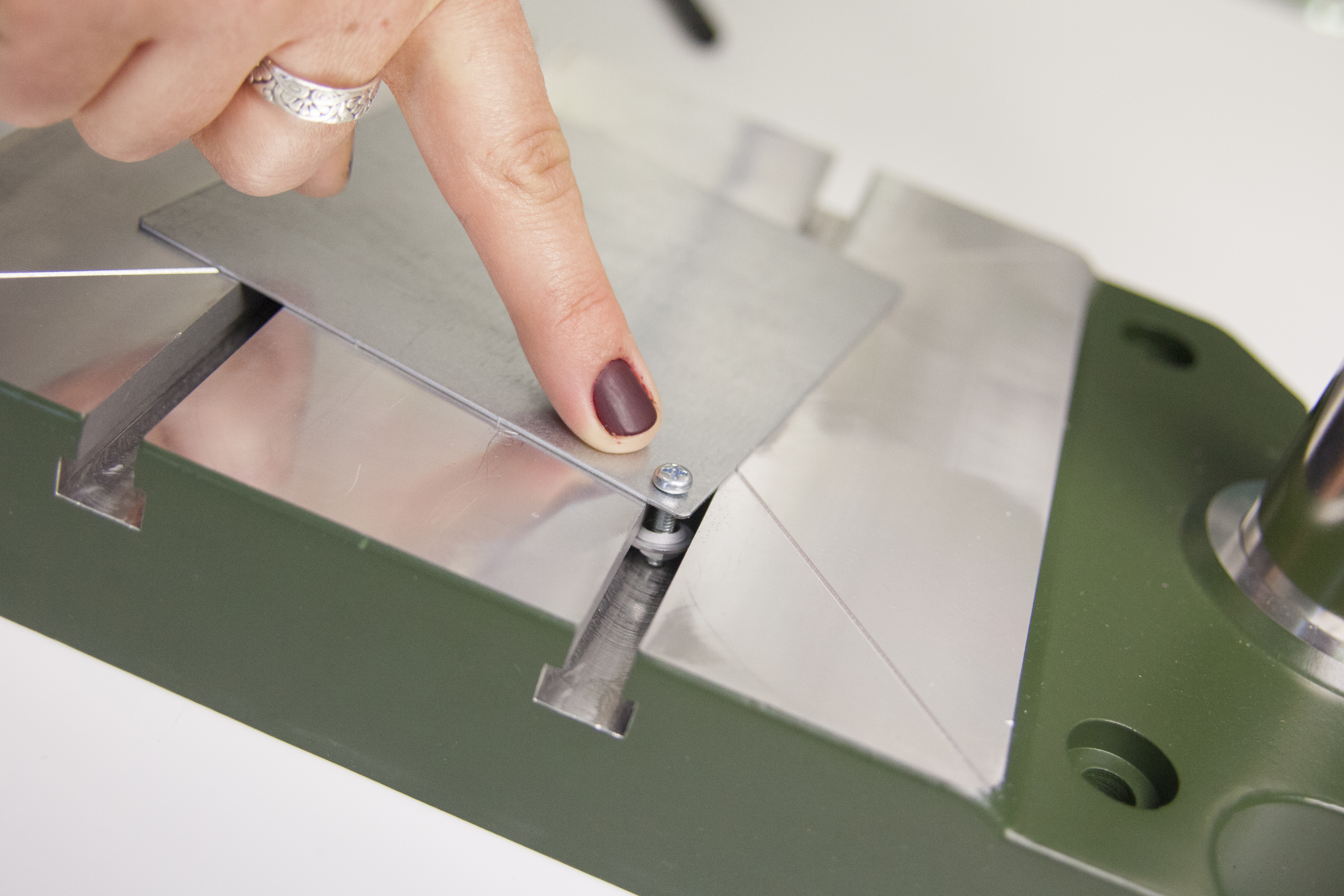
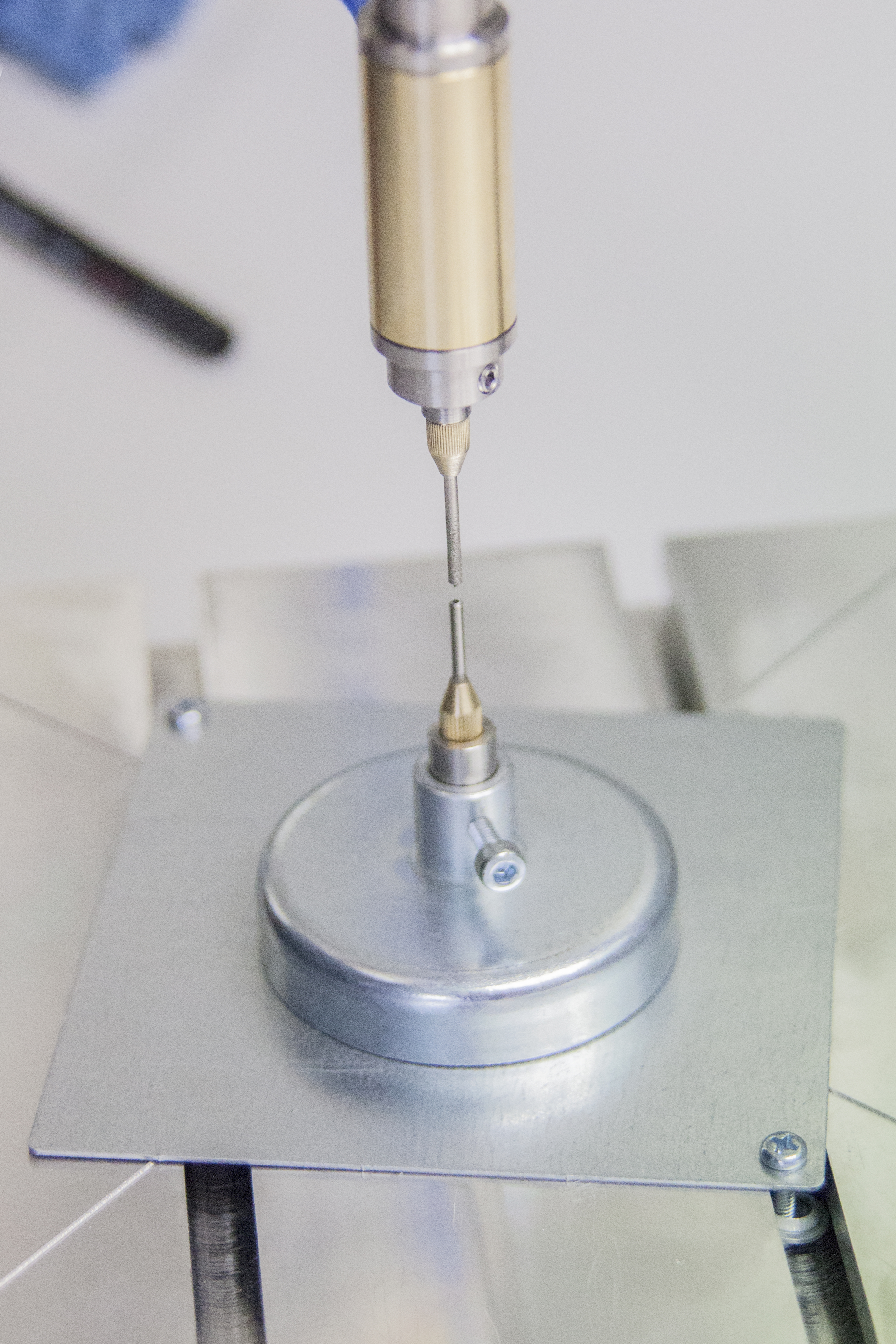
Step 5
Now place the drilled glass piece with the drilled side on the counterpart and carefully drill further into it. The glass piece can not slip away.
To prevent the diamond drill bit from drilling onto the counterpart, the depth stop on the drill (if present) can be set to about 1/10 of a distance.
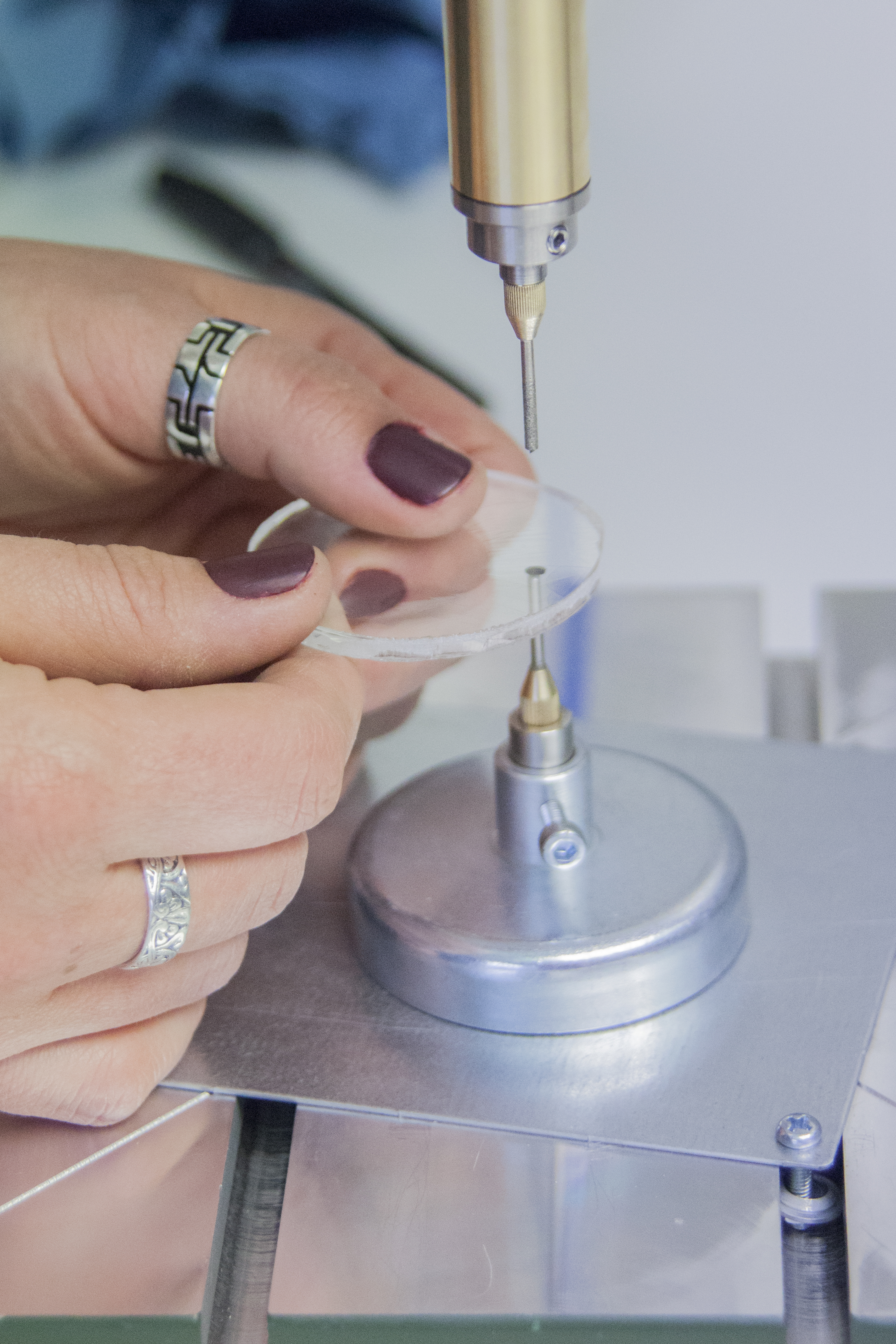
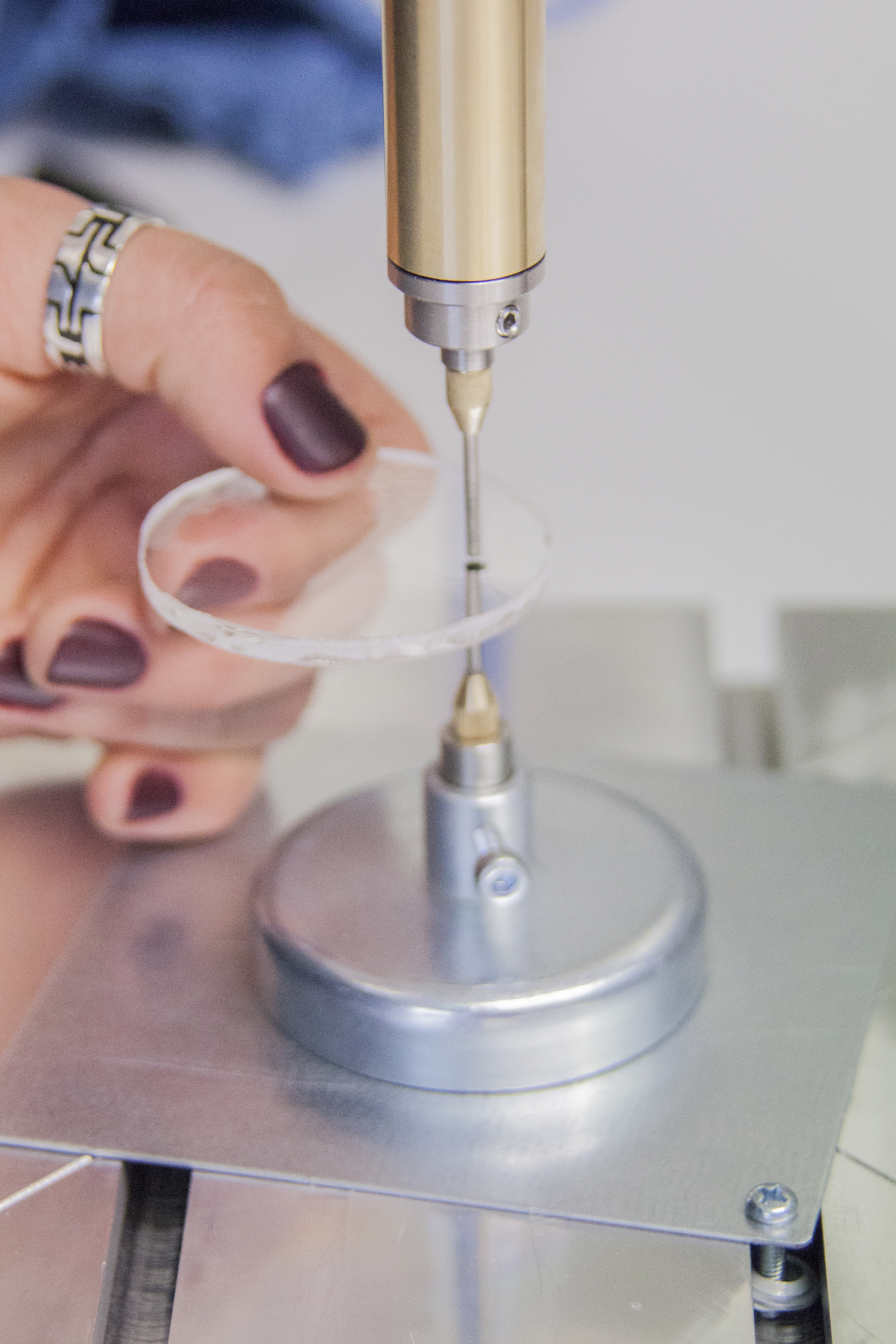
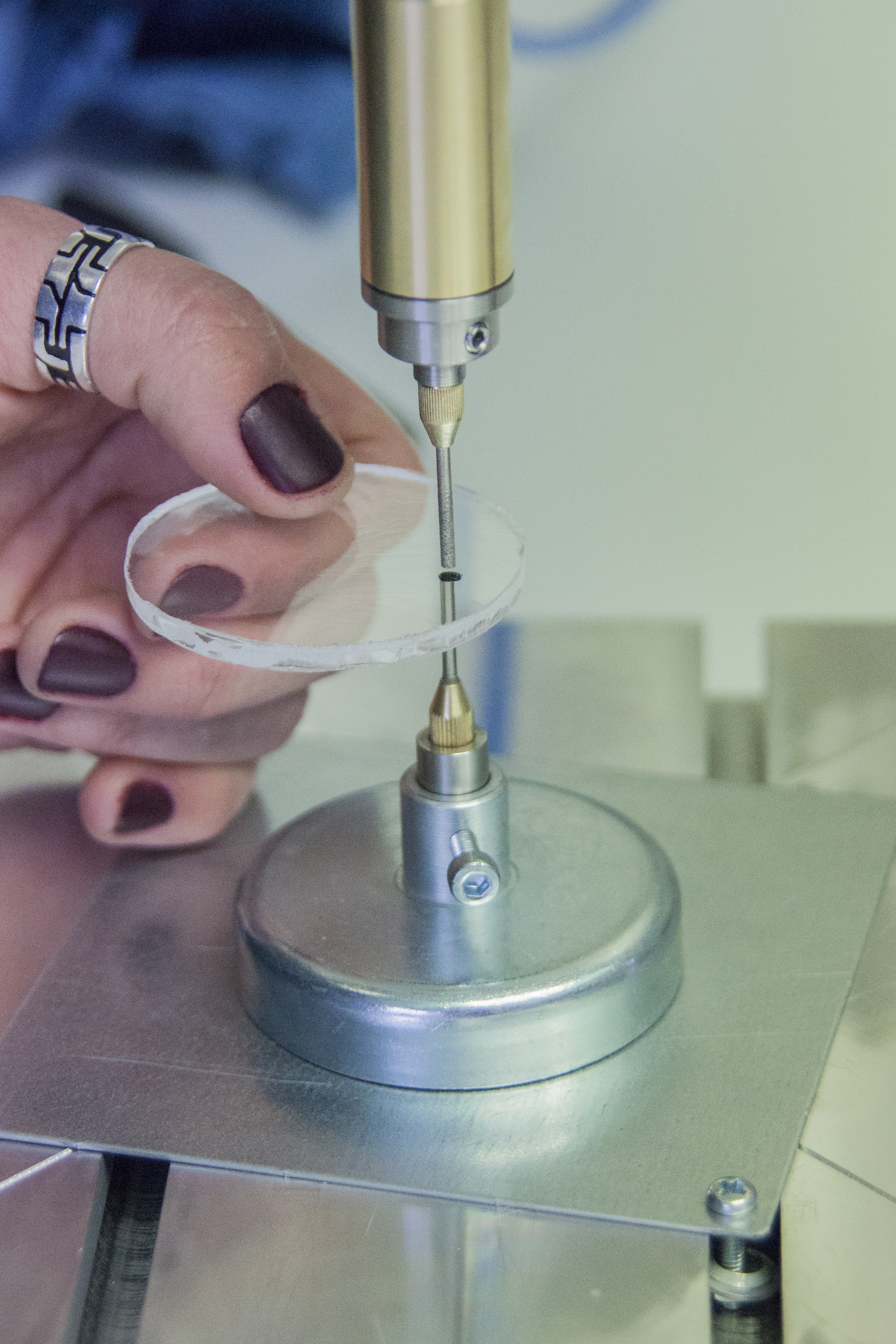
Tips and Tricks
The counterpart should be as long as possible so that the glass does not rest on the brass part (threaded piece). Otherwise it may happen that the glass breaks off at the drill entrance. Should it be difficult to drill the glass piece because of the protruding ejection needle, you can first drill the glass without ejection needle from both sides and reuse the ejector needle to pierce.
Important: For each new drill, drill it 2-4 times in the white sharpening stone before starting drilling, repeat this procedure if the drill is dull. It should be mentioned at this point that drilling with diamond hollow drills is not drilling in the usual sense (such as drilling metal or wood) but is a through-grinding of the workpiece.
Therefore, it is important to ensure that the drill does not get too much pressure to allow the water to pass through while drilling and flush out the drilling mud. Also you should not pierce in one, but always air to 1-2mm drilling depth, so that the ejector needle can eject the core. If the core is not ejected, remove the drill and loosen the core by hand.