
- 7705448 BULLSEYE TEKTA 1100-48F-48
- 3541115 Bullseye Frits 1122 01 F fine
- 3540849 Bullseye Frits 1125 08 F powder
- 3540815 Bullseye Frits 1122 08 F powder
- 3540835 Bullseye Frits 1120 08 F powder
- 3596000 Plastic jar sifter for 50 g VE:10 pcs
- 3128000 NIKKEN glass cutter NC-X03 wide 2-6mm
- 3211500 Running pliers PRP-1
- 3551227 Cerablanket 128 61x36,6cm, 50mm thick
Step 1
Draw the petals of the frangipani on your glass and cut them out. The petals do not have to be the same size or completely regular!
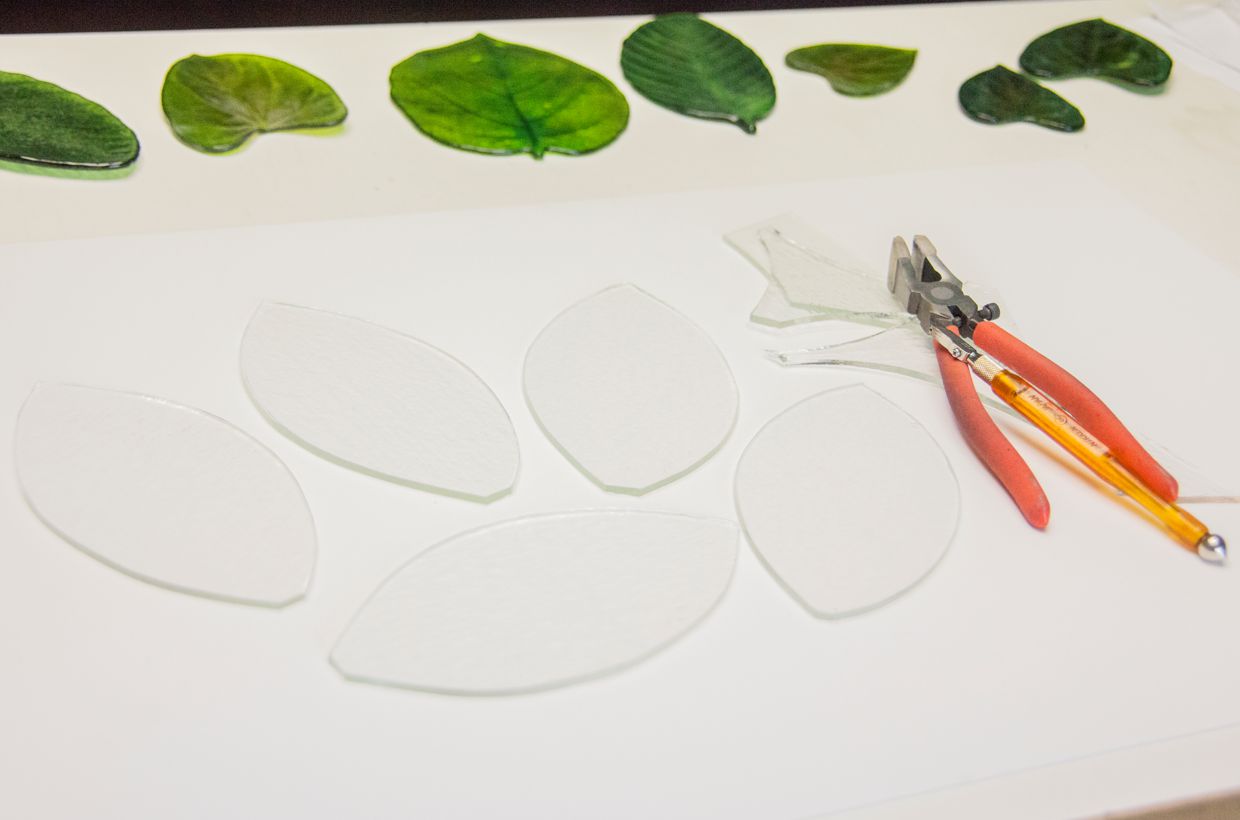
Step 2
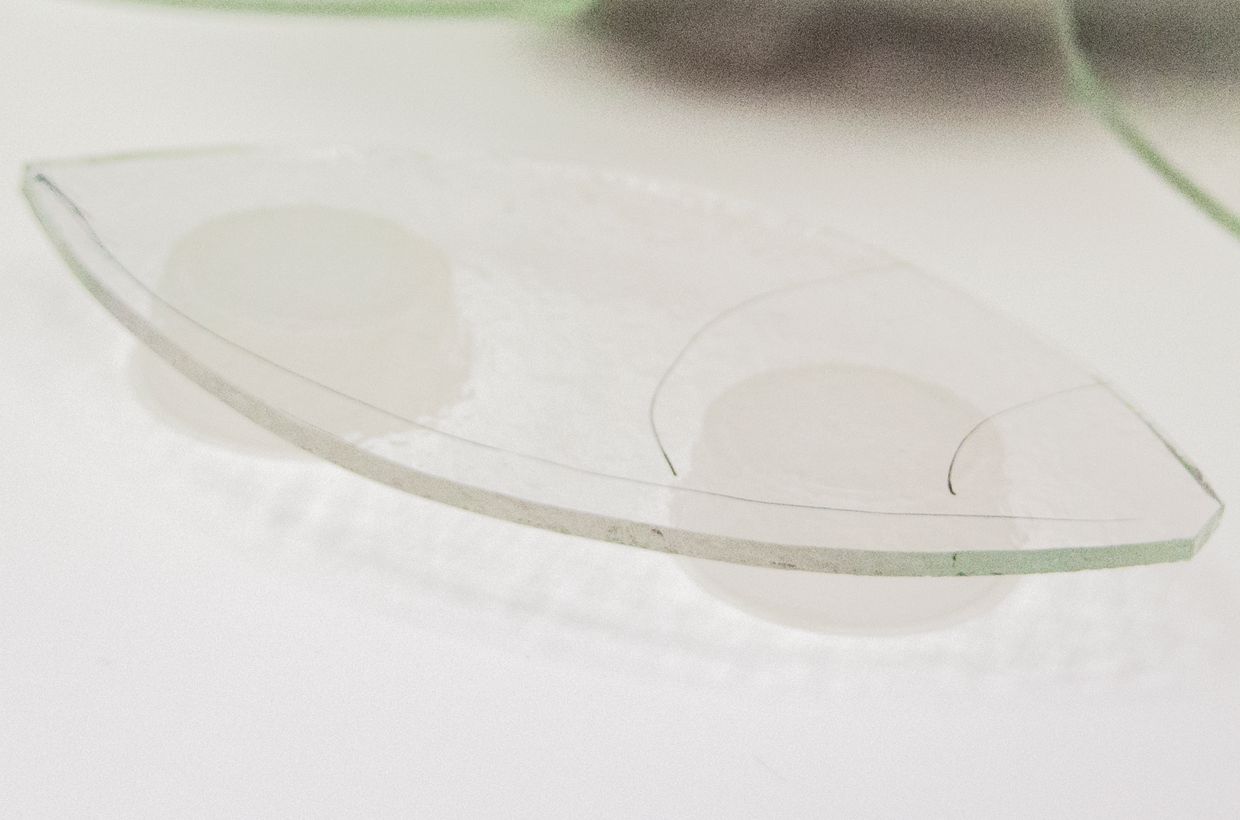
Sketch the different color areas. Now spread on the powder on the larger area in yellow, orange and red.
Step 3
Now brush off the powder on the side of the flower. Apply the yellow powder there. It is advisable to hold the sifter slightly at an angle. So you can apply the powder more precisely.
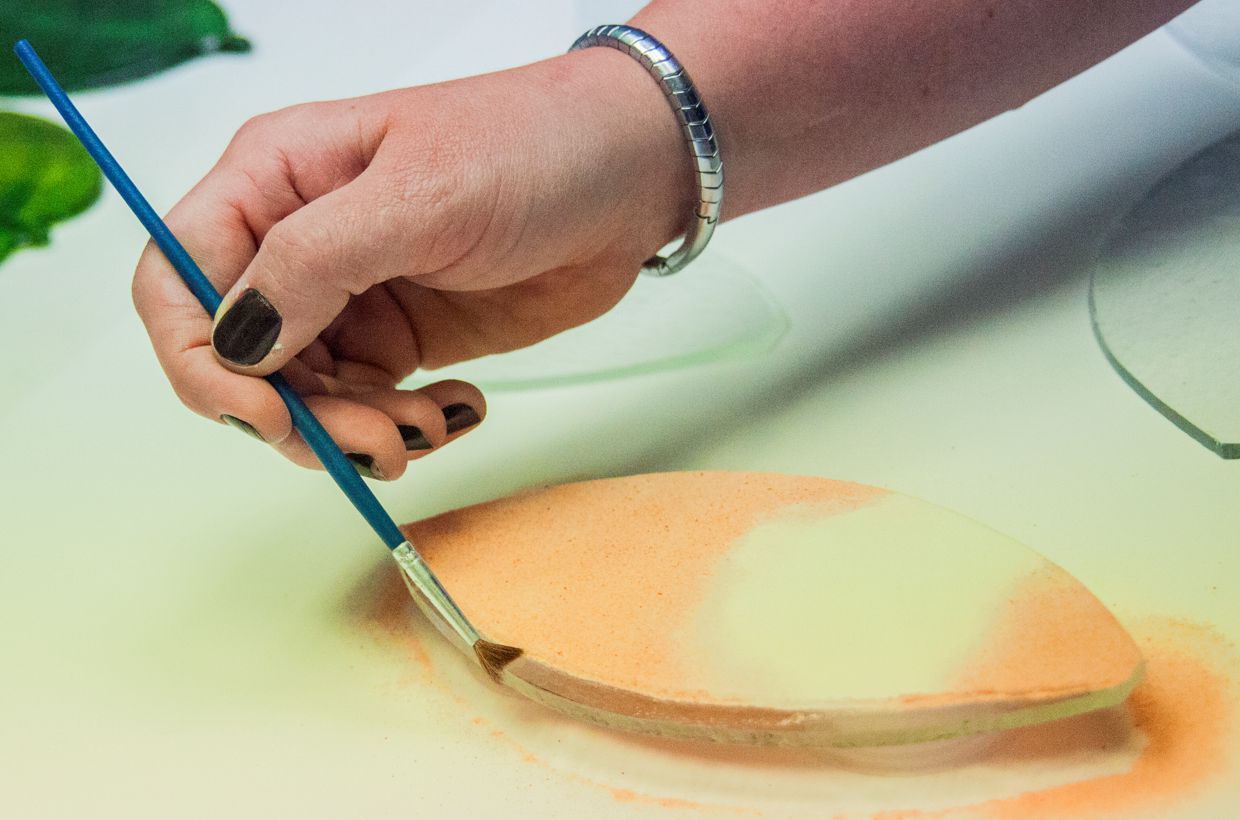
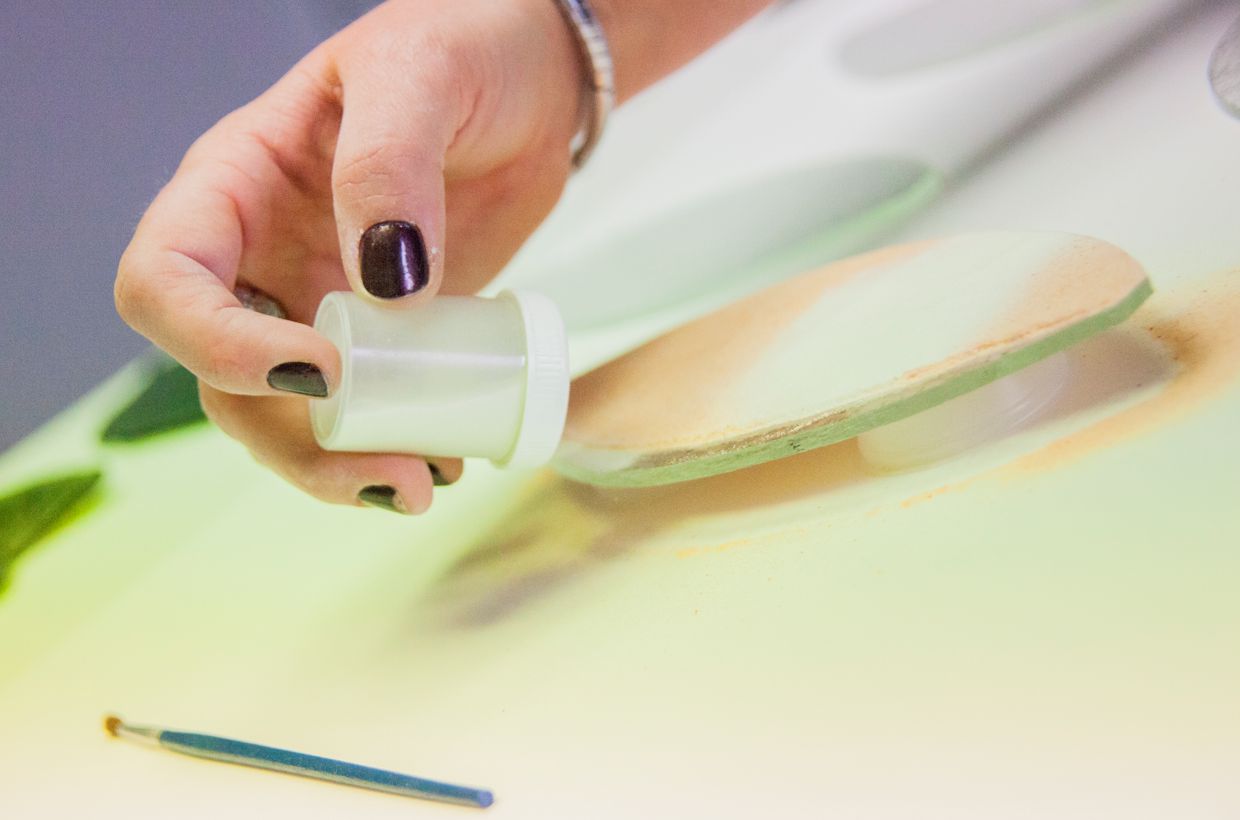
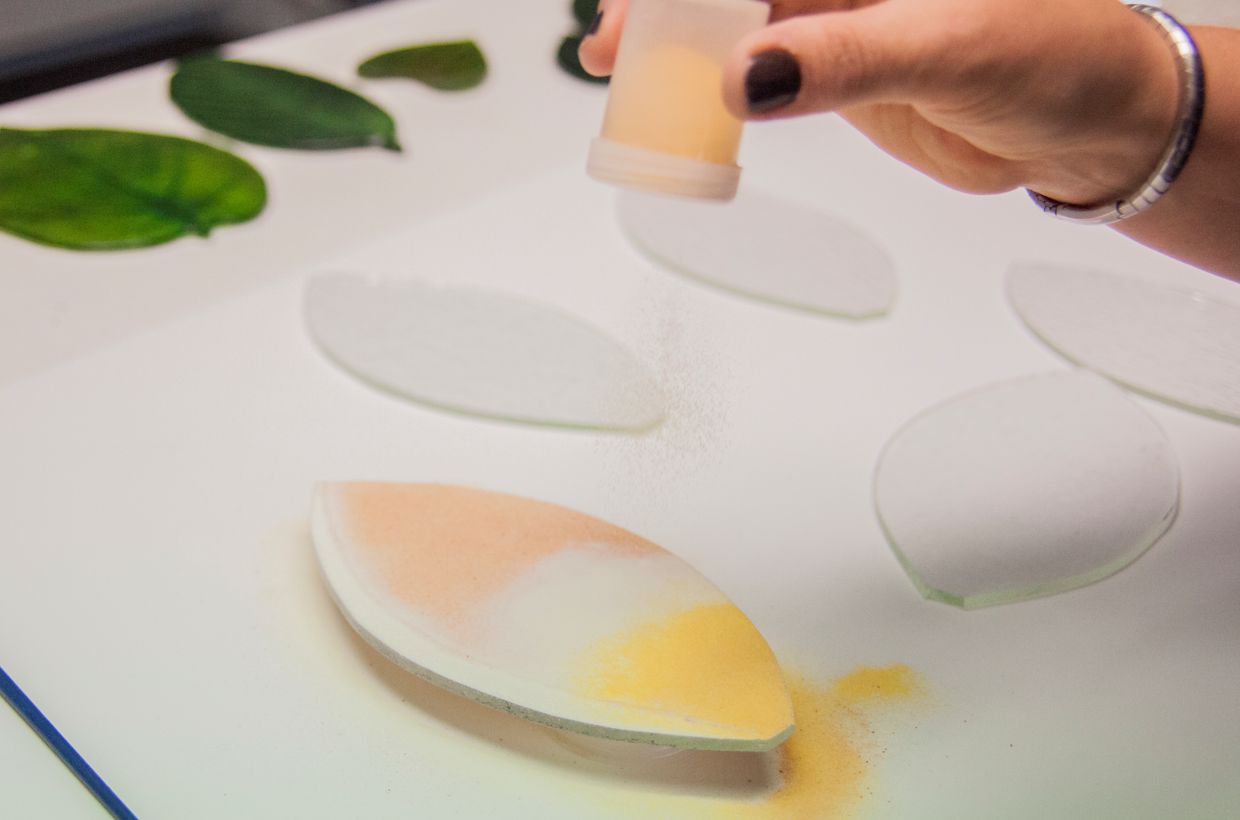

Step 4
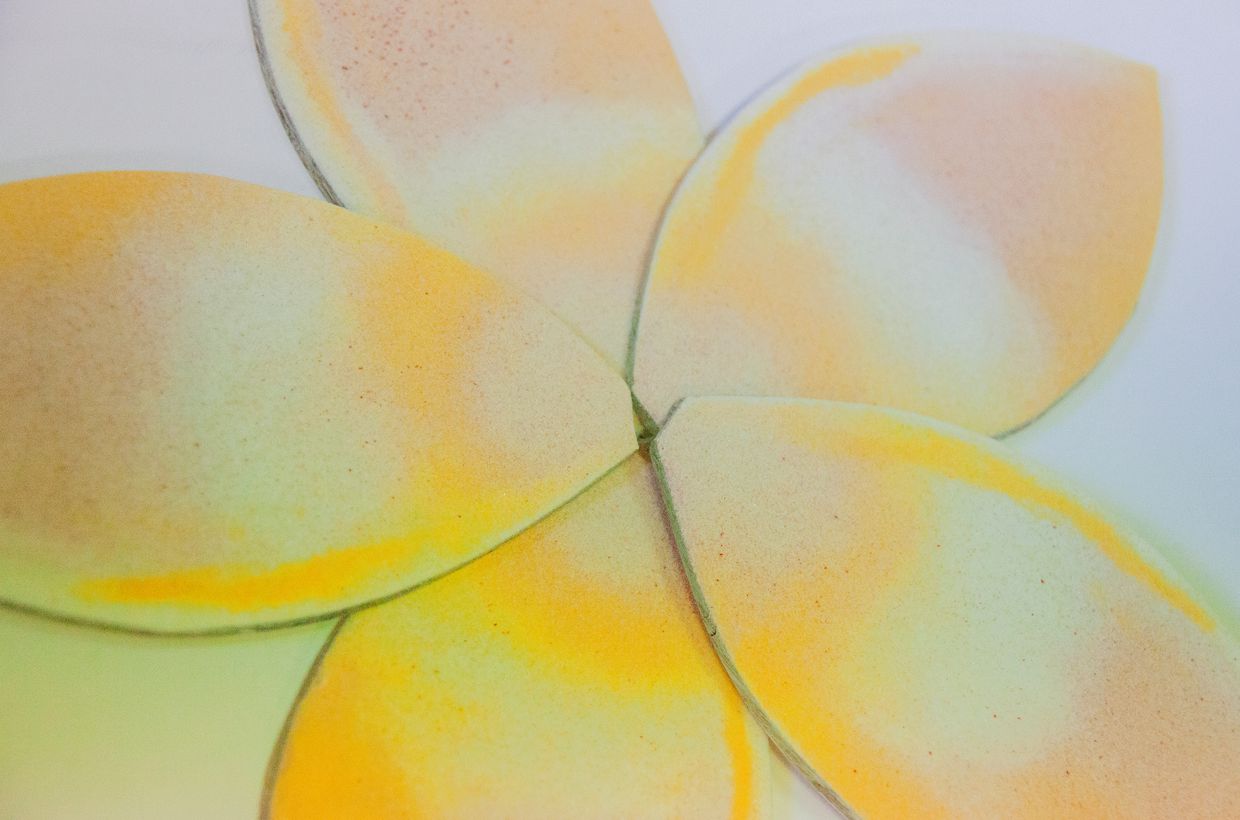
When each petal is done, carefully put them all together on a piece of bullseye paper in the kiln. Place the petals very carefully on top of each other and try not to change the powder layer. A few fine frits are sprinkled in the middle to emphasize the center of the flower.
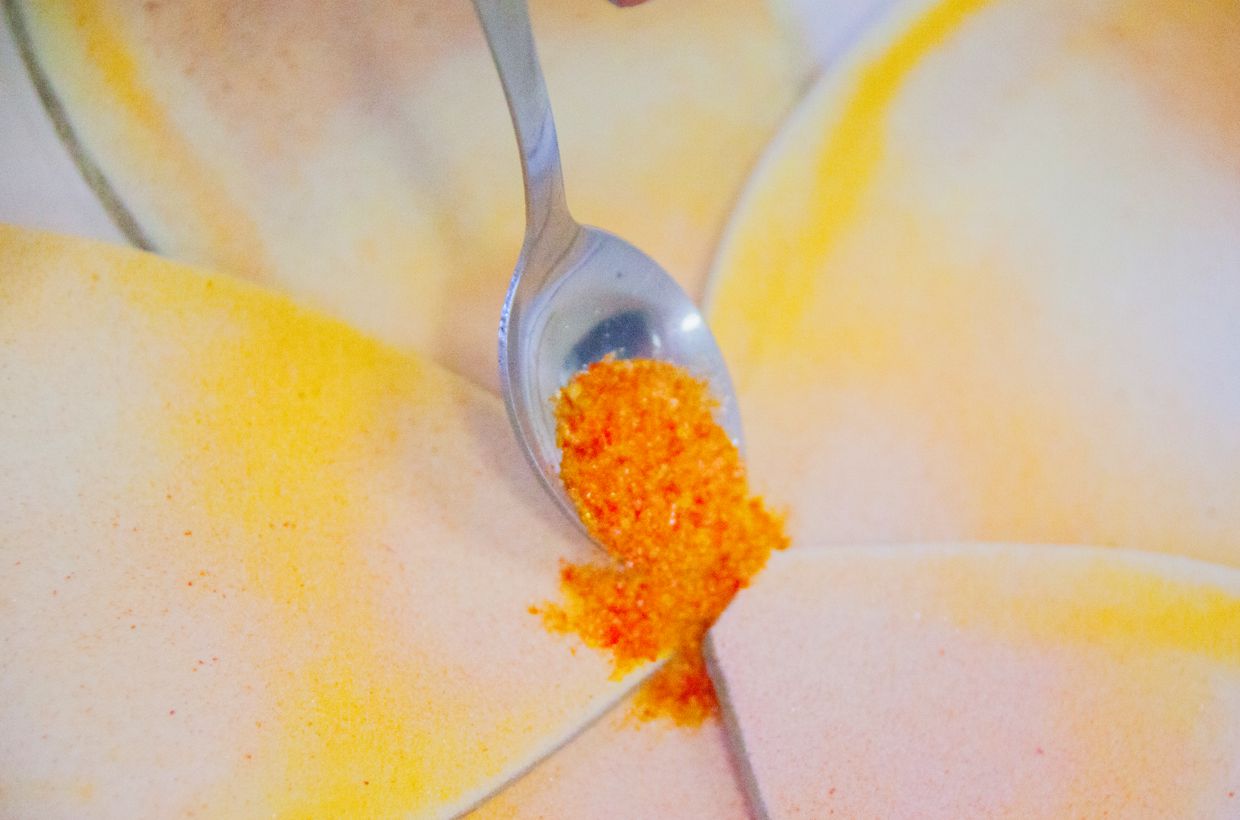
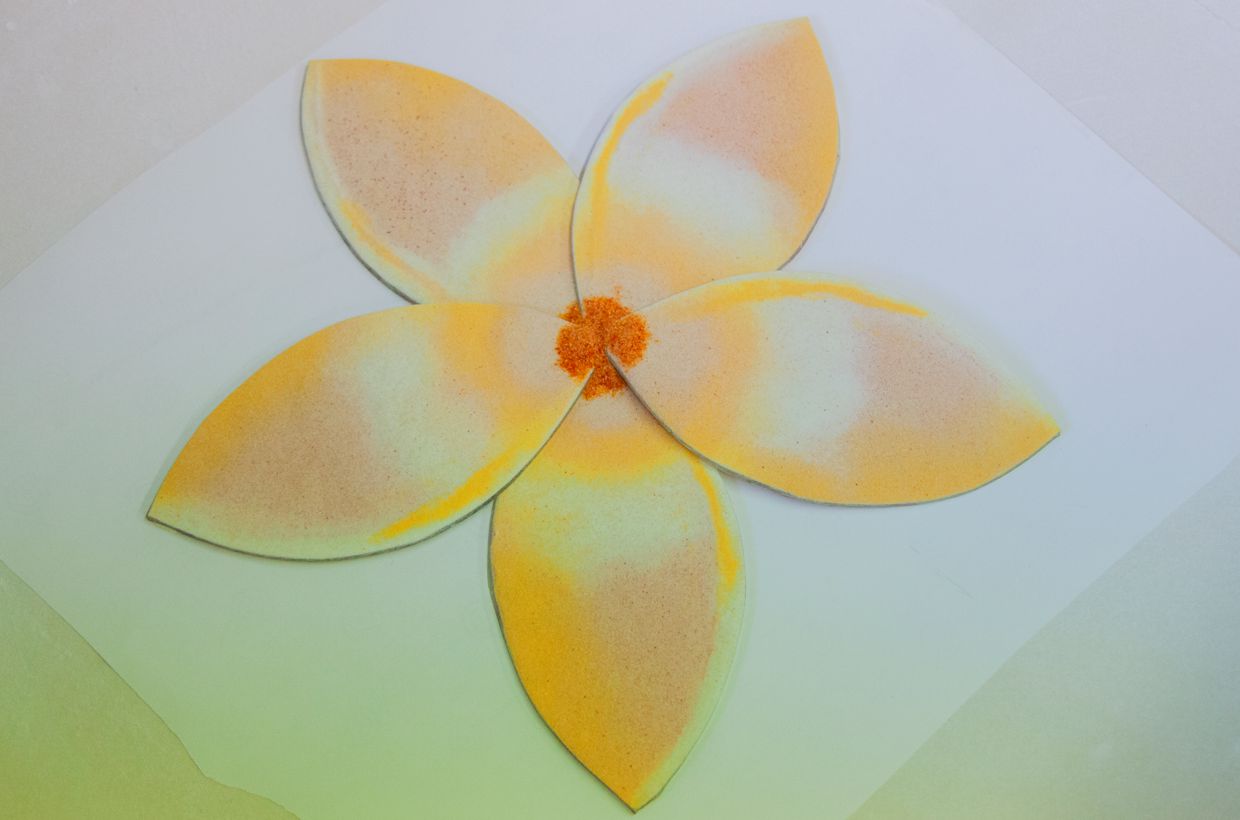
Firing cycle*
1) 120min - 500°C - 0min
2) skip - 795°C - 20min
3) skip - 520°C - 120min
4) 120min - 460°C - 0min
5) End
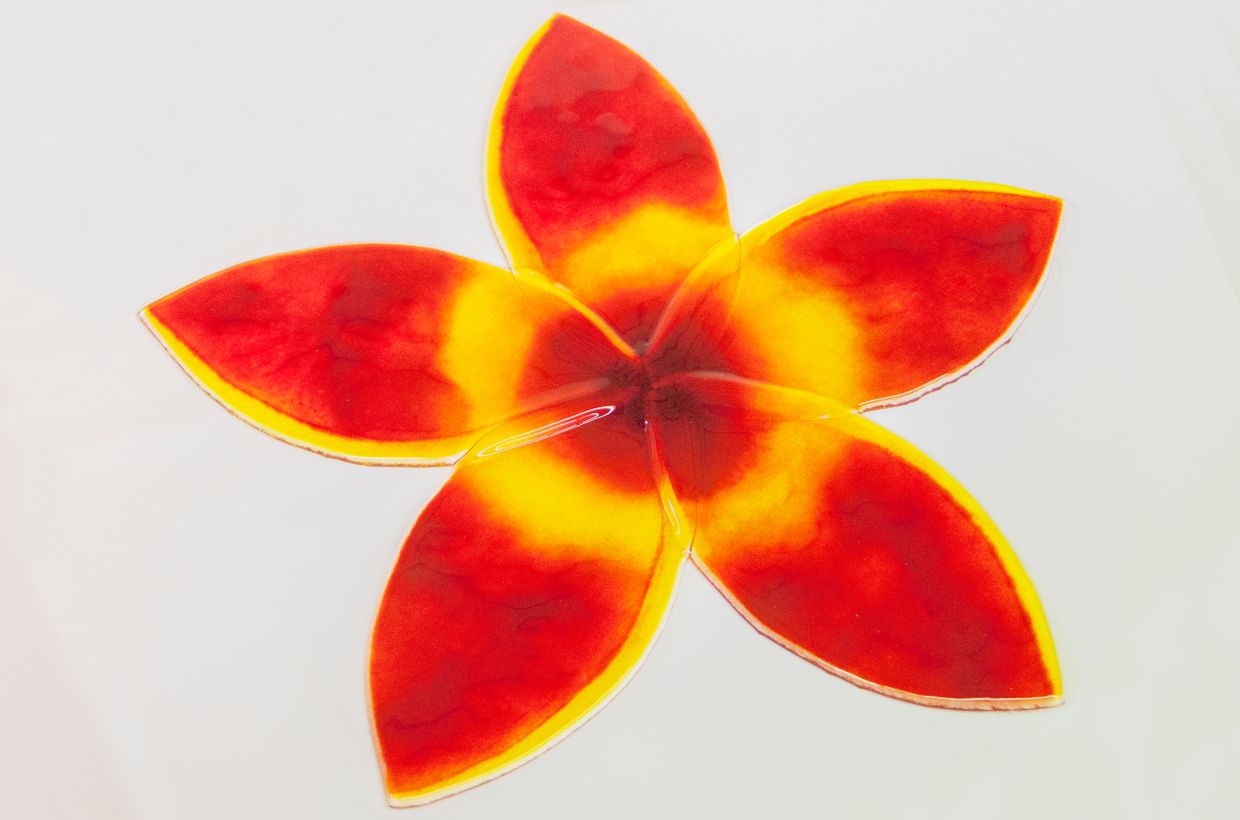
Step 5
After melting, the flower is slumped into the shape. To do this, take a suitable slumping mold. e.g. 3522558 or 3522524. Roughly cut the cerablanket into pieces like a petal (cut it a little larger) and divide it into thinner layers. These can then be shaped well and draped in the slumping mold. Create a "negative form" of the flower by crumpling or folding the pieces a little. Then you can put the flower on and slump it.
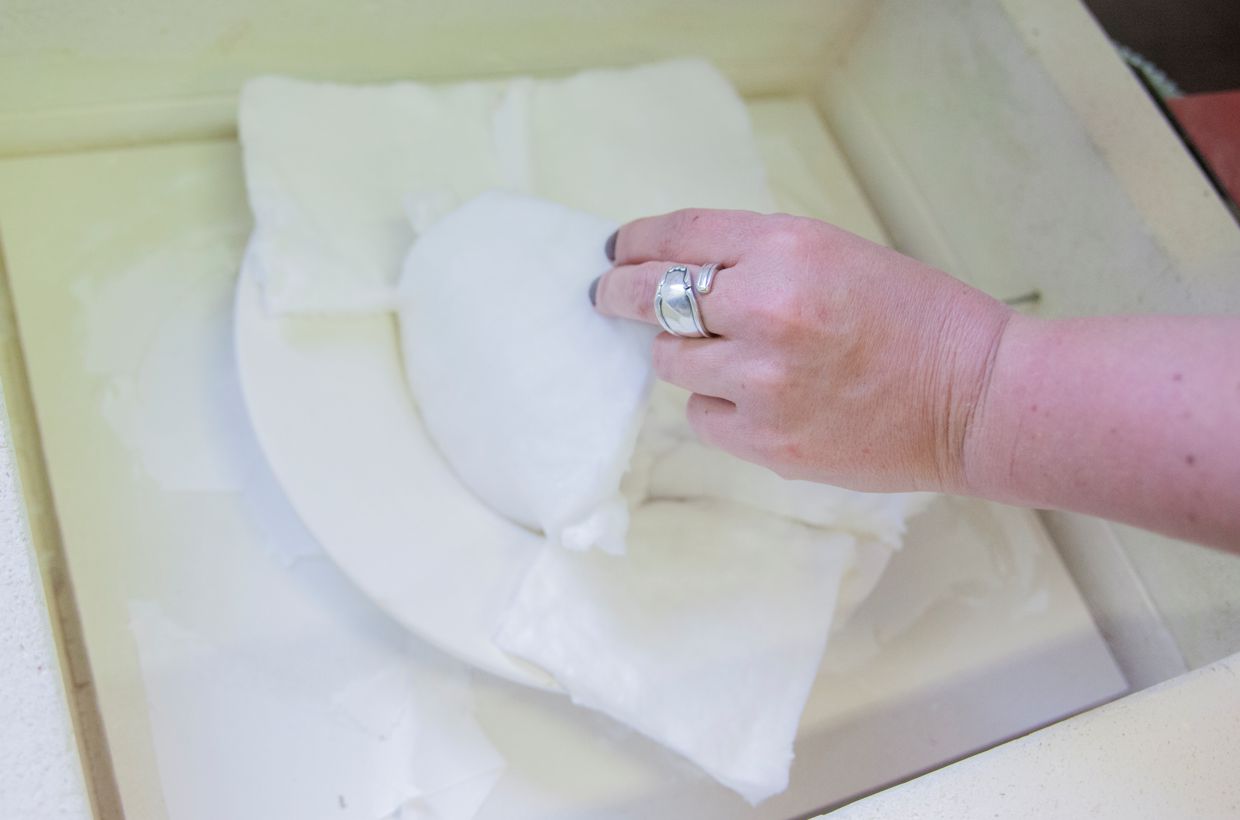


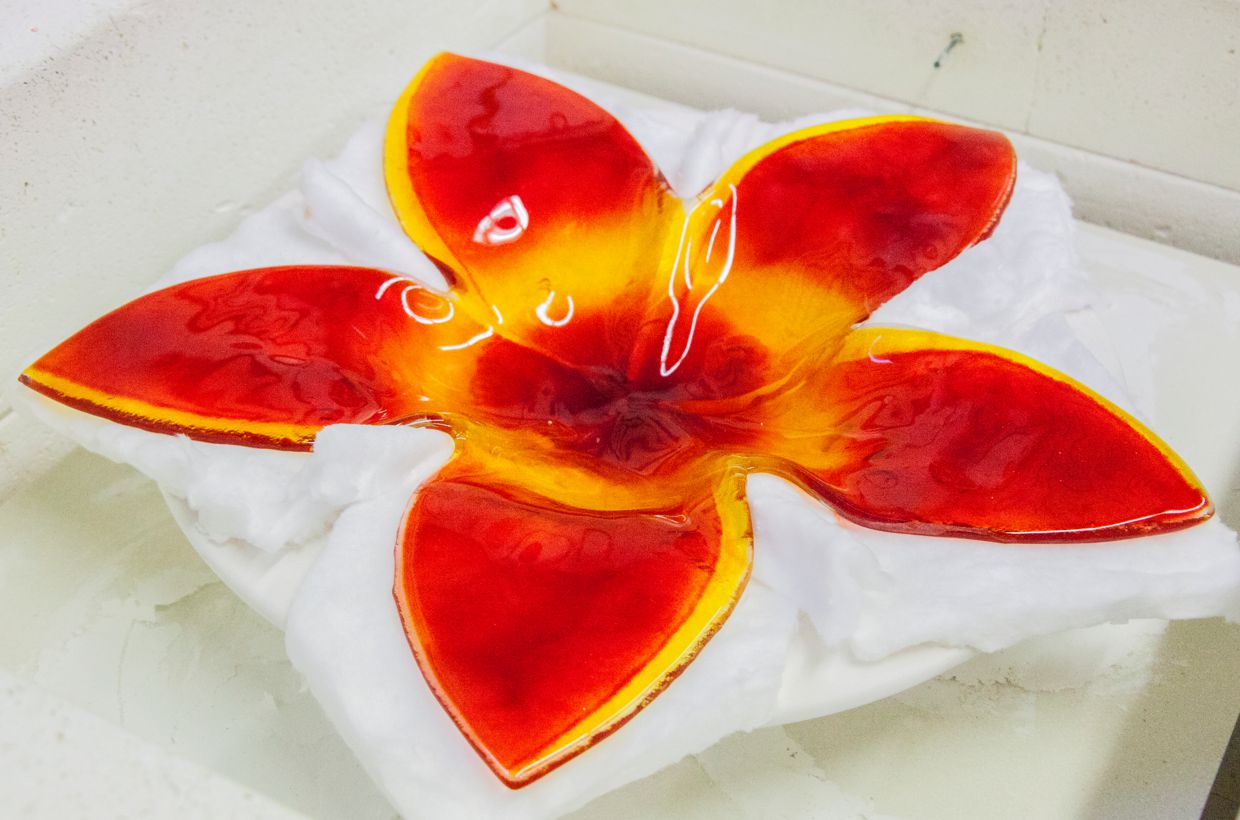
Firing cycle*
1) 120min - 500°C - 0min
2) skip - 700°C - 30min
3) skip - 520°C - 120min
4) 120min - 460°C - 0min
5) End.
* All information without guarantuee / fusing temperatures must be adapted to the respective kiln
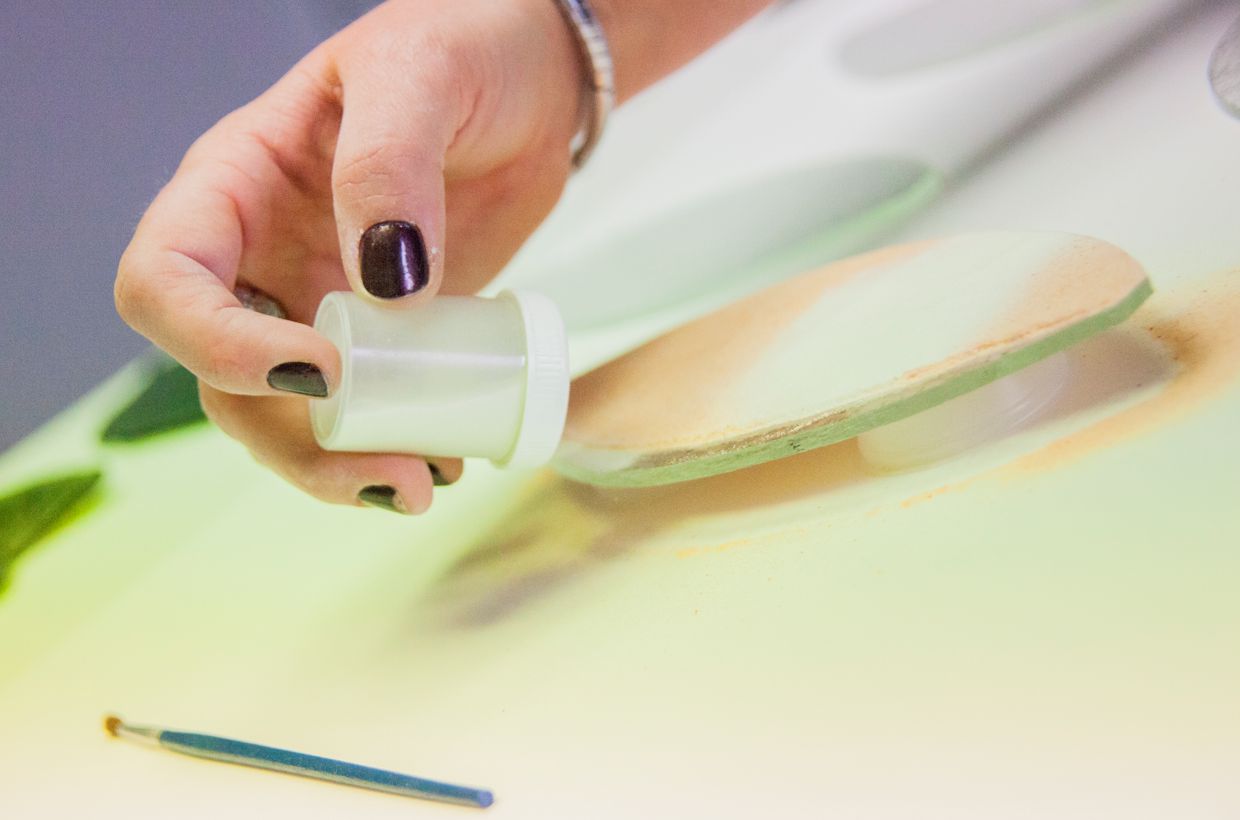
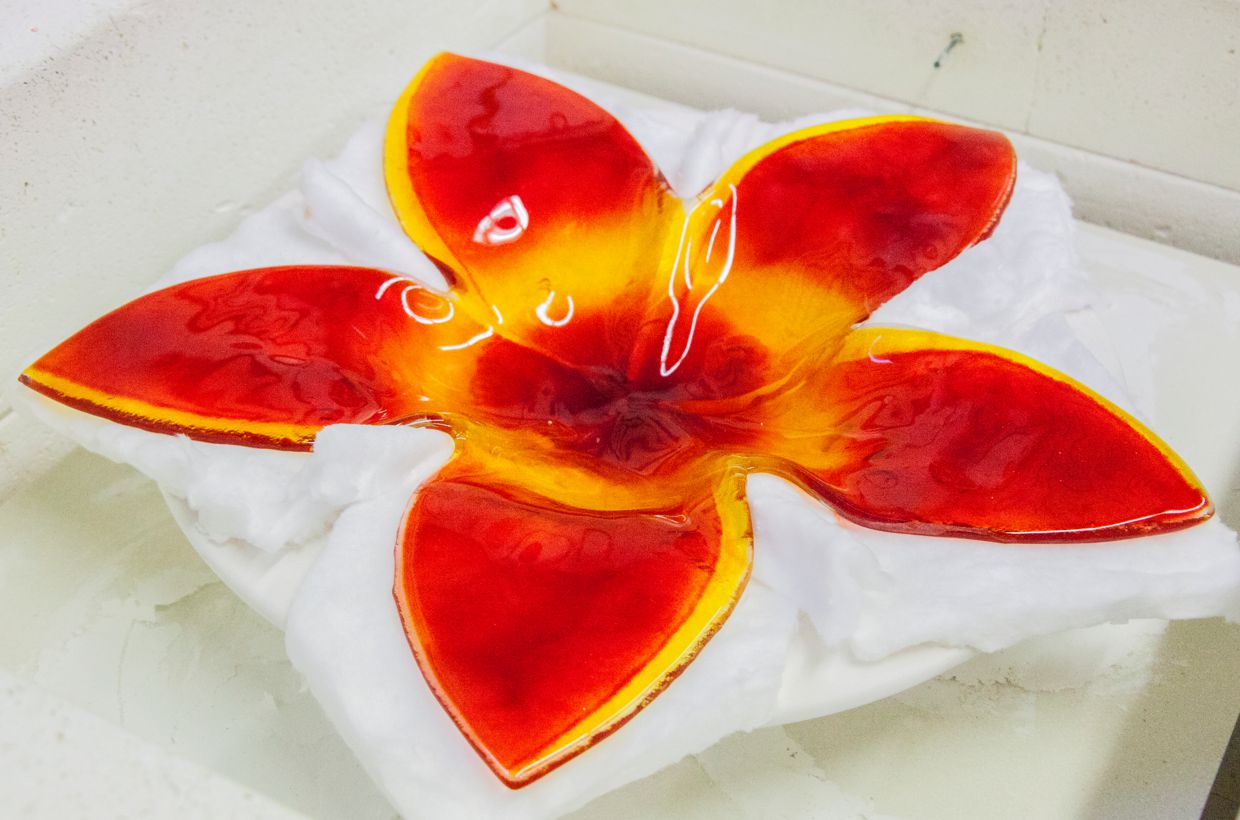
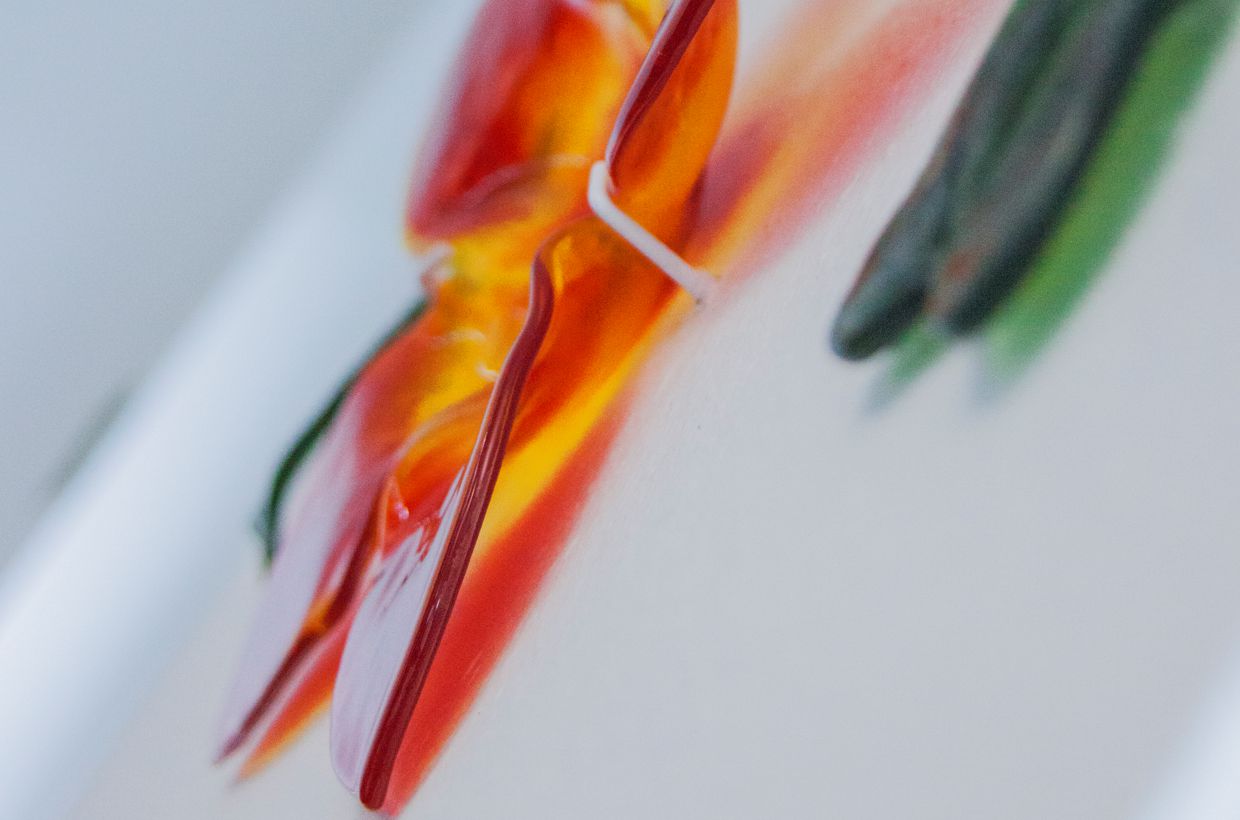
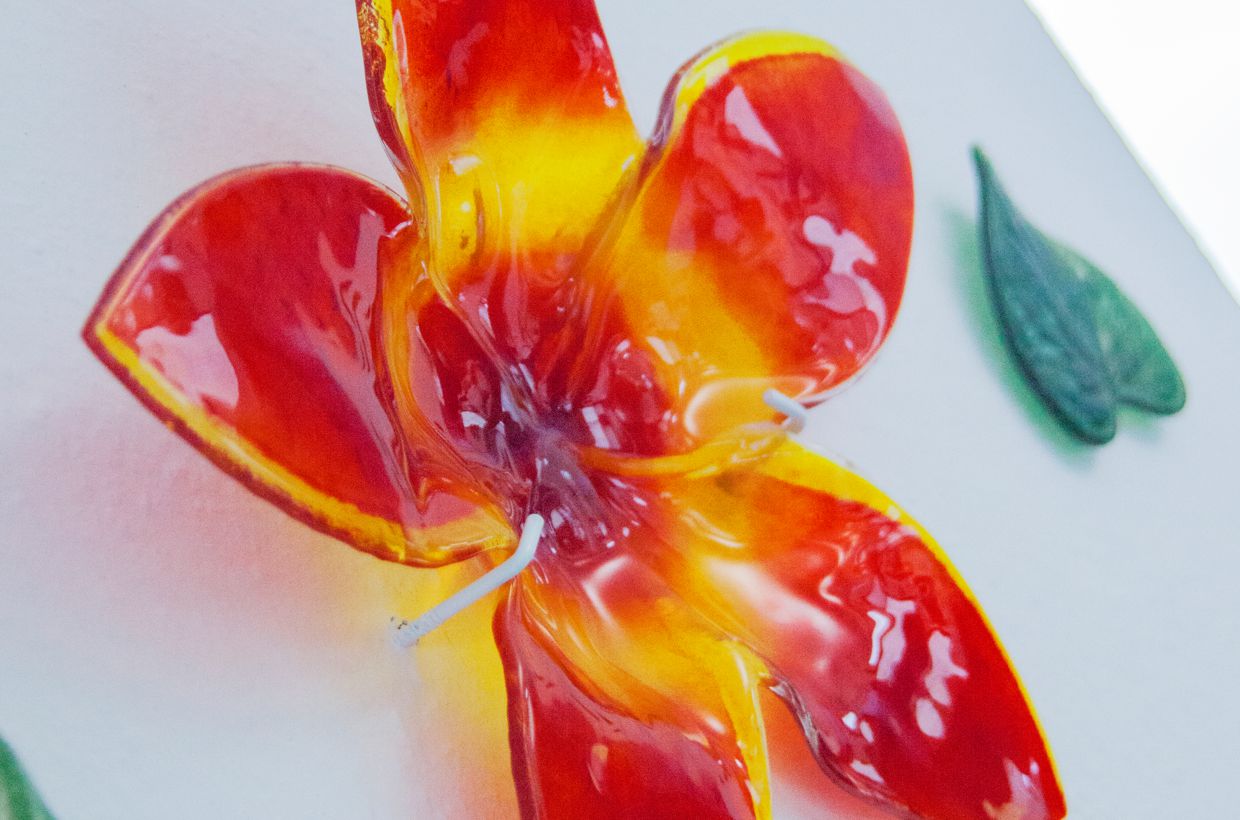